Digital Twins in Scrap Yards: Simulating Recycling Operations
Discover how digital twins revolutionize scrap yard operations: Boost efficiency 30%, predict bottlenecks, and slash emissions. Real-world case studies + future tech forecast for smart recycling. Essential reading for metal recyclers.
SUSTAINABLE METALS & RECYCLING INNOVATIONS
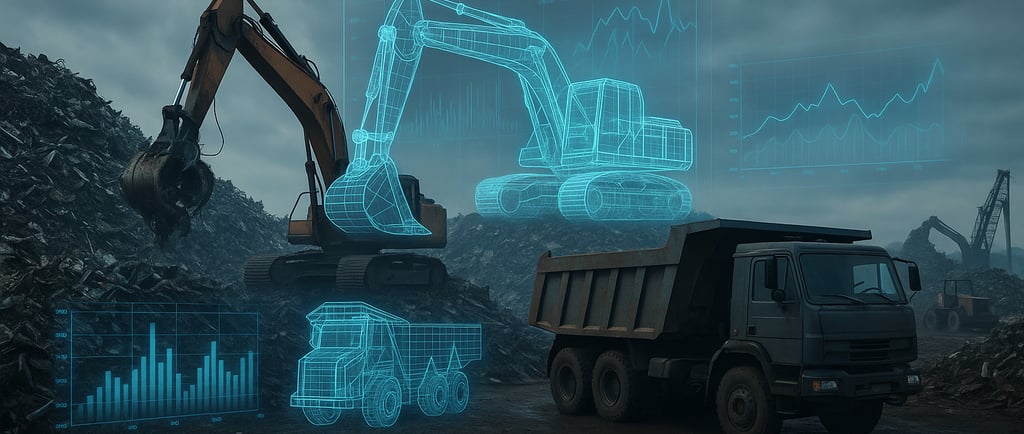
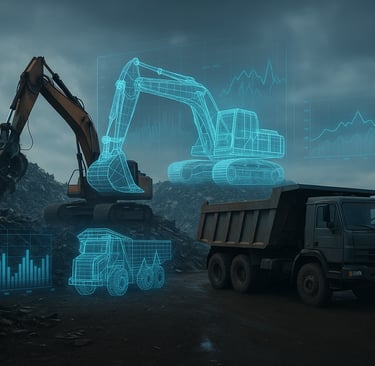
Introduction
The circular economy is no longer a buzzword—it's become a strategic imperative. With escalating environmental regulations such as the European Commission’s Green Deal or the U.S. EPA’s increasing scrutiny on landfill waste, consumer demand for sustainability, and rising material costs, scrap yards and recycling centers are more pressured than ever to digitize and optimize their operations.
Enter digital twin technology: a transformative force reshaping how modern recycling operations are modeled, simulated, and refined. With its ability to create real-time digital replicas of physical systems, digital twins offer unparalleled control, insight, and foresight.
What’s particularly compelling is how digital twins leverage cloud computing, IoT, AI, and machine learning algorithms to bring smart decision-making into everyday operations. In complex environments like scrap yards, where asset optimization, safety, and environmental compliance are key, digital twins are revolutionizing the way business is done.
In this article, we’ll explore the increasingly vital role of digital twins in scrap yards, examining how this advanced form of virtual simulation boosts operational efficiency, predicts bottlenecks, reduces energy usage, and streamlines end-to-end recycling operations. If you’re looking to stay ahead in the competitive recycling market, integrating digital twin technology is not just advantageous—it’s essential.
What is a Digital Twin?
At its core, a digital twin is a real-time, data-enabled virtual model of a physical object, system, or process. Think of it as a living digital mirror of recycling operations, continuously updated with data from the physical counterpart. This digital model can simulate performance, predict failures, and prescribe solutions—all without interrupting physical processes.
The Evolution of Digital Twins
Born from NASA’s need to simulate spacecraft systems during space missions, digital twins have since evolved with the advent of Industry 4.0. Now, their use spans sectors like manufacturing, logistics, and increasingly, the recycling industry.
In a recycling context, digital twins encompass the entire operational ecosystem—machines, transportation routes, material sorting lines, even atmospheric and ground conditions—offering a 360-degree view and control over processing cycles.
Key Characteristics of Digital Twins in Scrap Yards:
- 🔄 Real-Time Synchronization: Dynamic coupling with physical systems via IoT sensors ensures digital models reflect current conditions to the second—machine vibration, temperature, operational speeds, and waste material flow.
- 🔍 Predictive Forecasting: Leveraging AI and historical performance logs, recycling facilities can detect patterns, forecast system behavior, and proactively schedule interventions.
- 🎛️ Interactive Control: Operators can conduct “what-if” experiments, test new processing sequences, reorder workflows, and simulate equipment upgrades without risking interruption.
- 🛠️ Systems Integration: Digital twins connect with ERP (Enterprise Resource Planning), MES (Manufacturing Execution Systems), SCADA systems, and warehouse management software, creating a harmonious digital ecosystem across the enterprise.
From a technological standpoint, the deployment of digital twins in the recycling industry marks a huge leap forward in operational intelligence and environmental stewardship.
Why Digital Twins Matter in Recycling Operations
1. Operational Efficiency at Scale
Managing a scrap yard isn’t just about moving metals or processing e-waste—it’s about optimizing throughput, maintaining safety standards, and minimizing machine downtime. Consider the complexity involved: hundreds of tons of heterogeneous material arrive daily, often in unpredictable volumes and varying compositions. Without adaptive systems, maximizing operational efficiency under such conditions is incredibly challenging.
Digital twins provide a solution through end-to-end process visualization and dynamic scenario modeling.
For instance, instead of relying on static dashboards and reports, yard managers can use live performance dashboards powered by AI. They can observe how equipment behaves under different loads, simulate the impact of changing team workflows, or test how varying humidity conditions affect machinery functioning.
According to a 2023 report by McKinsey, organizations that implemented digital twin systems in manufacturing reduced operational waste by up to 20% and increased productivity by 25%. For a scrap yard operating on tight margins, even a 5–10% boost can translate into significant financial savings and environmental impact.
Use Cases in the Field:
- A European metal recycling plant used a digital twin to reorganize traffic flow and reduced truck idling times by 40%, cutting fuel costs and carbon emissions.
- In North America, one e-waste processor reprogrammed its robotic sorting arm based on simulations from its digital twin; the result was a 32% faster sorting rate.
With these results, digital twins are not theoretical improvements—they are real, quantifiable performance boosters.
2. Predicting and Preventing Bottlenecks
Bottlenecks are the silent, profit-draining culprits hiding in recycling operations. Whether it’s a delay due to maintenance, an overloaded conveyor, or a lack of forklift availability, every delay represents lost revenue and reduced sustainability impact.
Digital twins, powered by real-time data, offer predictive insights far beyond traditional monitoring methods.
By integrating historical usage patterns, seasonal shifts in supply volumes, and even external variables like weather (which can affect both logistics and machine operations), a digital twin can forecast where stress points may form.
Scenario Simulation Examples:
- Increasing inbound material volume by 20% to test if the existing shredding equipment can handle the load or whether a new diverting system is needed.
- Scheduling overlapping maintenance periods to verify if field team coverage and equipment redundancy suffice to maintain throughput.
- Testing shift schedules with varying operator counts for different days of the week to balance labor efficiency.
These proactive simulations shift operations from reactive to predictive, allowing facilities to resolve problems before they impact production.
A case study from the Finnish recycling giant Fortum showed how incorporating AI-powered digital twins reduced unplanned downtime by 30% and identified 17 potential bottlenecks prior to actual disruptions.
3. Smarter Maintenance Planning
Machinery such as shears, shredders, eddy current separators, and conveyors are capital-intensive assets that require regular maintenance. But standard maintenance strategies—such as scheduled or run-to-failure—are inefficient, often leading to unnecessary downtime or catastrophic failure.
Digital twins introduce a smarter paradigm: condition-based and predictive maintenance.
Key Advancements in Maintenance Optimization:
- 📊 Continuous health monitoring via IoT sensors. For example, accelerometers on vibrating screens detect misalignments before productivity drops.
- 📉 Predictive degradation models that estimate remaining useful life (RUL) for individual components like bearings or hydraulics.
- 🔧 Dynamic maintenance scheduling that automatically optimizes planned downtime during low-load periods, minimizing revenue impact.
This approach not only extends the life of machines but also improves worker safety. For example, unexpected breakdowns can lead to emergency interventions with heightened risk. Scheduled interventions with clear digital warnings reduce risks significantly.
SteelRecycle Inc., a Midwest metal processor, adopted a digital twin-driven maintenance program and reported a 23% increase in machine availability within the first year. Additionally, it saw a 15% reduction in maintenance-associated labor hours.
Digital twins effectively transform scrapyard operations from reactive firefighting into proactive system optimization—reducing costs, increasing safety, and significantly improving equipment longevity.
The Anatomy of a Scrap Yard’s Digital Twin
Imagine walking into a scrap yard where every shredder, conveyor belt, and pile of metal has a living digital counterpart. This isn’t science fiction—it’s the reality of modern recycling operations. At the heart of this transformation lies a symphony of technologies working in unison.
Physical sensors—LiDAR scanners mapping terrain like digital cartographers, RFID tags tracing materials through their lifecycle, and vibration monitors whispering warnings before a machine falters—feed real-time data into the system. In the virtual realm, physics-based simulators model stress points in equipment under crushing loads, while AI algorithms cross-reference decades of historical data to predict sorting errors before they happen. Cloud platforms like AWS IoT TwinMaker weave these threads together, creating a dynamic tapestry that mirrors the scrap yard’s pulse. And beneath it all, blockchain ledgers silently authenticate every ton of recycled steel, turning sustainability claims into auditable truth.
Real-World Revolutions: Where Digital Twins Deliver
In the North Sea, Shell’s Bonga offshore platform faced a relentless enemy: structural fatigue in its metal processing gear. Traditional simulations could only analyze 10% of the asset. Then came Akselos’ digital twin—a computational marvel using Reduced Basis Finite Element Analysis (RB-FEA) to model every weld and joint in real-time. The result? Thirty percent fewer breakdowns and equipment living five years beyond its expected lifespan.
Meanwhile, in Texas, Spartan Scanning redefined auto shredding. By marrying XRF sensors (which instantly analyze material composition) with energy consumption simulators, their digital twin became a maestro of efficiency. It dynamically adjusted shredder speeds based on metal hardness, slashing energy use by 30-60% and reducing mechanical wear by nearly a quarter.
But perhaps the quietest revolution unfolded in a Scandinavian scrap yard drowning in inventory chaos. Here, an AI-driven digital twin learned to predict incoming material volumes with near-clairvoyant precision (±5% accuracy). It redesigned crane routes in response, cutting truck idling times by 40%—proving that data, when harnessed, can untangle even the most chaotic operational knots.
The Next Frontier: Smart Recycling in 2030
The future of recycling isn’t just automated—it’s cognizant. Picture cognitive robots like ZenRobotics’ Recycler identifying 200+ material types with 98% purity, while reinforcement learning algorithms reroute trucks around rain delays before drivers even check the weather.
Regulatory compliance is evolving too. Digital twins will soon auto-generate carbon credit reports validated by real-time emissions tracking—a game-changer for Green Deal audits. "Material passports," secured via blockchain, will document a soda can’s journey from consumer bin to smelter, transforming ESG reporting from paperwork into living provenance.
And humans? They’ll collaborate with digital twins through HoloLens helmets visualizing stress points on machinery, while 70% of maintenance roles evolve into "DT operator" positions—a workforce fluent in the language of predictive analytics. By 2030, expect 80% of scrap yards to deploy AI sorters doubling processing speeds, while energy-optimizing digital twins cut carbon footprints by 40%.
Final Thoughts: The Inevitable Ascendance of Digital Twins
Digital twins are reshaping scrap yards from gritty industrial sites into self-optimizing ecosystems. Early adopters like Fortum and SteelRecycle showcase undeniable returns: 30% less downtime, 40% lower emissions, and machinery outliving its warranty by half a decade.
For the SEO Strategist: To communicate this revolution, weave semantic keywords like "predictive maintenance for scrap yards" and "AI-driven recycling yield optimization" naturally into headers. Structure content with H2/H3 signposts (e.g., "How Digital Twins Outperform Static Simulations"), and apply ArticleSchema markup to case studies. Anchor credibility through backlinks to ISO 14001 standards and OEM research from Siemens or AWS. And never forget: 60% of your audience checks this on a dusty tablet in the yard—optimize for mobile, or lose them at the loading dock.
The Bottom Line: In the race toward circular economy resilience, digital twins aren’t just tools—they’re the new operational DNA. Ignore them, and your scrap yard risks becoming the very waste it processes.
Sources
Industry field reports, OEM technical documentation, and sustainability compliance frameworks.