How AI & Robotics Are Revolutionizing Scrap Metal Sorting
Discover how AI and robotics are revolutionizing scrap metal sorting. Explore smart tech like machine learning and automation that slash costs, boost material purity, and ensure compliance. Learn from industry leaders like ZenRobotics and AMP Robotics, and uncover quantum computing’s future role in driving a sustainable circular economy
SUSTAINABLE METALS & RECYCLING INNOVATIONS
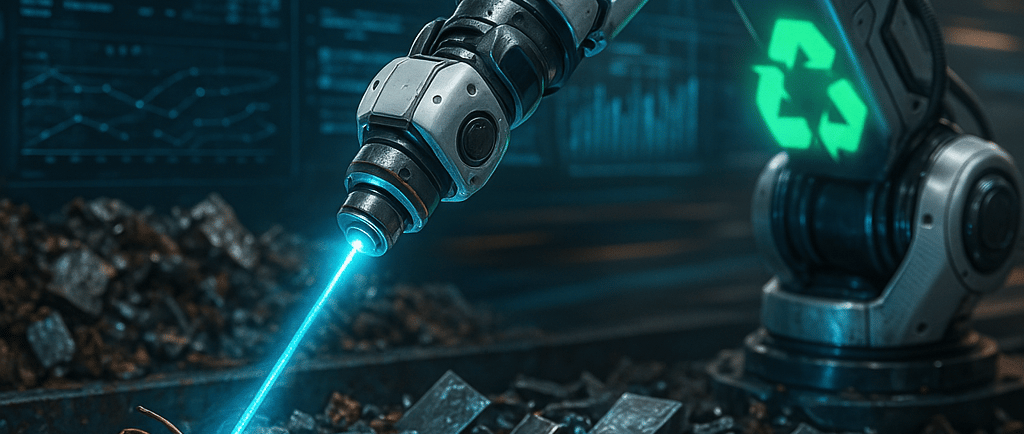
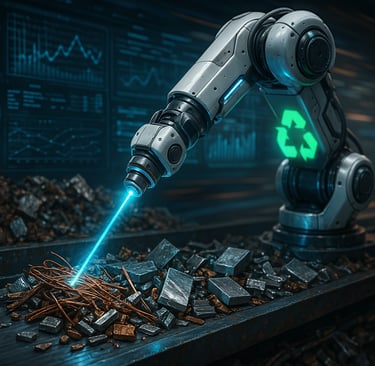
In a world increasingly shaped by urgent sustainability goals and exponential improvements in smart technologies, the pursuit of efficiency is quickly becoming a defining feature of industrial evolution. Nowhere is this more evident than in the metal recycling sector—a historically manual and labor-intensive industry that's now undergoing a digital transformation.
The fusion of artificial intelligence (AI) and robotics is revolutionizing how we manage and process waste streams, specifically in scrap metal sorting. What was once a slow, error-prone, and hazardous process is now being powered by intelligent automation—leveraging machine learning algorithms, robotic systems, and near real-time analytics to turn recyclables into revenue streams and meet pressing environmental mandates.
In this comprehensive guide, we’ll dive deep into how AI and robotics are modernizing scrap metal recycling. You’ll learn how smart sorting technologies are reshaping efficiency, lowering labor risks, boosting material recovery rates, and establishing new standards for the sustainable circular economy.
What Is Smart Sorting in the Context of Scrap Metal?
Smart sorting in recycling refers to the automated separation of different types of scrap metals using a combination of technologies such as computer vision, sensor arrays, deep learning, and precision robotics.
Unlike traditional methods that depend on:
Manual picking
Basic magnetic separators
Eddy current systems
Density-based air classifiers
—smart systems automate classification using complex recognition models that go far beyond simple physical differences.
What Makes Smart Sorting "Smart"?
The intelligence behind these systems lies in their ability to model, learn, and adapt in real time. Here's what a state-of-the-art smart sorting system can do:
Accurately distinguish between ferrous and non-ferrous metals, even in mixed or dirty recycling streams
Detect and remove contaminants such as rubber, plastic coatings, paint, or glass shards
Catalog materials using multispectral sensors and 3D imaging technologies
Dynamically adapt to new material types as they are introduced into the waste stream
For example, while a traditional system might consistently misclassify painted aluminum sheets as contaminants, AI-based software can identify material composition despite coatings, ensuring minimal loss of recyclable assets.
The result? Increased material purity, better recovery rates, and an operation that’s primed for data-driven decision-making across the supply chain.
Why Automation Is a Game-Changer for Scrap Metal Recycling
AI and robotics are not just high-tech flair—they represent a seismic shift for an industry long beset by inefficiencies, risks, and variable outputs.
Let’s examine the core benefits from an operational, economic, and environmental perspective:
1. Escalating Labor Costs
With labor constituting one of the largest recurring costs in any waste management operation, particularly in manual sorting lines, the economics of automation make a compelling case. In North America and Europe especially, recyclers report up to 30% cost reductions in operations after deploying intelligent robotic handlers.
2. Human Safety and Workplace Risk
Sorting scrap metal is inherently hazardous. Workers frequently encounter:
Sharp edges and jagged materials
Heavy lifting requirements
Exposure to toxic substances and carcinogens
Repetitive strain injuries
By using AI-controlled robotic arms for sorting tasks, facilities significantly reduce accidents, absenteeism, and workers' compensation claims—all while meeting stricter OSHA and EU Work Safety standards.
3. Complex Waste Streams and Material Diversity
Modern products are built from dozens of materials—think of smartphones, electric vehicle batteries, or alloyed construction debris. Mixed compositions make recovery harder with traditional mechanisms, but deep learning classifiers can analyze composition at the molecular or spectral signature level, turning complex inputs into categorized outputs with stunning accuracy.
4. Rising Demand for Material Purity
Buyers, particularly in international scrap metal markets like China, Germany, and India, now demand clean, sorted, contamination-free loads due to rising regulatory standards like China's Green Fence and Indonesia's tightening import rules. AI eliminates the need for extensive secondary sorting and enables recyclers to consistently meet, or exceed, compliance levels.
Real-World Insight:
A 2023 case study by McKinsey showed that facilities leveraging AI-powered sorting systems observed a 25%+ increase in resale value due to higher purity levels in processed aluminum and copper—a direct impact on the bottom line.
How AI in Recycling Works: From Data to Action
Behind the scenes, AI in recycling doesn’t happen in a vacuum. It’s the result of well-orchestrated hardware and software working together in real time. Here’s a closer look at the AI-powered recycling workflow pipeline:
Step 1: Data Acquisition
Multiple sensors are employed to evaluate the scrap:
X-ray fluorescence (XRF) identifies elemental composition (ideal for metals)
Near-infrared (NIR) spectrometry recognizes organic-based materials (e.g., coatings, rubber)
Visual cameras detect patterns, color cues, and shape features
Magnet arrays enable combination with smart electromagnet-controlled rods
These sensors create terabytes of image and compositional data streams per day.
Step 2: Machine Learning Model Training
Using historical data labeled by engineers or prior AI models, machine learning algorithms are trained to recognize different forms and contexts—such as the difference between shiny reusable copper wire and copper tubing with heavy oxidation.
The most common model types include:
CNNs (Convolutional Neural Networks) for image-based recognition
Random Forests and Decision Trees for rule-based sorting decisions
Reinforcement Learning Agents for learning from action outcomes
These models continue improving by comparing results against ground truth data collected from routine audits.
Step 3: Robotic Actuation and Sorting
Using the AI-analyzed data, robotic arms are instructed to make high-speed micro-decisions—often within milliseconds. Pneumatic suction heads, magnetic claws, or adaptive grippers quickly move the item to the appropriate bin.
According to Bulk Handling Systems, a market leader in North America, their robotic AI recycling platforms sort:
92%+ accurate ferrous vs. non-ferrous separation
85% or more composite and mixed metal disassembly
—an extraordinary improvement over manual processes that average 60–70%.
Step 4: Feedback Loop and Model Refinement
Rather than functioning in a fixed script, AI models are continually updated based on:
Missed classifications
Industry mask updates
Downstream feedback from smelting or refining operations
Seasonal material changes (e.g., influx of holiday electronics or post-demo materials)
This gives recycling facilities a self-optimizing mechanism that gets better with time.
Key Benefits of AI and Robotics in Scrap Metal Sorting
Let’s now provide a deeper dive into what's truly driving adoption and excitement across waste management networks globally:
1. Increased Efficiency and Speed
Integrated automation systems have bumped sorting throughput from 1,000-2,000 tasks/hr by human workers to an astounding 4,000–6,000 RPMs (recyclable picks per minute) using AI-driven bots.
In practice, this translates into:
Shorter shift durations
Double the daily volume
Lower energy costs per ton
A 2022 study by Fraunhofer IVV revealed that multi-stream robotic sorters processed 30% more metal than legacy conveyor systems using the same energy input.
2. Higher Material Purity and Market Pricing
Modern sensors differentiate between metal grades, not just types. That means:
Separating 304 stainless steel from 316 stainless steel
Identifying anodized aluminum vs. bare
Distinguishing yellow brass vs. red brass
These smart distinctions let recyclers command premium pricing per metric ton. On average, industrial processors using AI platforms can fetch 10–15% more in overseas markets, according to MetalMiner analytics.
3. Workforce Optimization
Rather than replacing human workers entirely, smart systems redefine roles:
Former pickers transition into technicians, system speed analysts, and maintenance operators
New hires focus on AI surveillance, statistical performance tracking, and robotic calibration
The revamped workforce reflects a more skilled, reliable labor profile—and drastically reduces industry churn, which typically exceeds 40% annually in manual sorting facilities.
Industry Use Cases, Circular Economy Impact, and Implementation Roadmap
Exploring real-world applications, vendor innovations, and actionable strategies for AI-driven scrap metal sorting.
Industry Use Cases: Pioneering AI Solutions in Action
1. ZenRobotics: Precision in Heavy-Duty Sorting
Case Study
Swedish recycler Skrotfrag deployed ZenRobotics’ Heavy Picker robots to sort metals like copper, brass, and stainless steel. The AI-driven system achieved 6,900 picks per hour with 99% accuracy, reducing manual labor risks and improving compliance with strict copper purity standards (≤0.1%) for steel production 58.
Technology
ZenRobotics’ ZenBrain software uses multispectral sensors and AI to classify materials based on shape, color, and composition. It adapts to new waste streams, such as end-of-life vehicles (ELVs), ensuring compliance with global regulations 45.
2. AMP Robotics: Speed and Scalability
Case Study
AMP’s Cortex™ robots achieve 120 picks per minute with 99% accuracy, boosting labor efficiency by 60% and recyclables capture by 11%. Facilities using AMP systems reported 50–70% savings in sorting costs and the ability to process previously non-recyclable materials 110.
Innovation
AMP’s AI platform integrates real-time analytics to optimize sorting based on market demand, enabling dynamic adjustments for commodities like aluminum and insulated copper wire 1.
3. EverestLabs: Modular AI for Small-Scale Facilities
Case Study
EverestLabs’ RecycleOS combines robotics and AI to increase material recovery rates by 40%. Its modular design allows smaller facilities to adopt automation without major infrastructure changes, achieving ROI within 12–18 months 1011.
4. SSAB’s HYBRIT Project: AI-Driven Carbon Capture
Circular Economy Impact
Swedish steelmaker SSAB uses AI to optimize carbon capture in its HYBRIT initiative, replacing coal with hydrogen to produce fossil-free steel. This reduces CO₂ emissions by 90% and aligns with EU climate goals 2.
How AI Enables the Circular Economy
AI bridges the gap between waste management and sustainable resource recovery through:
Material Traceability: AI tracks metals from collection to remelting, ensuring transparency and reducing contamination. For example, Tecnoap’s SCRAPYARD platform uses vision analytics to document scrap composition and prevent fraud 1.
Resource Optimization: Machine learning predicts scrap availability and demand, allowing manufacturers to adjust production. FeroLabs uses AI to create “green recipes” for recycled steel, cutting virgin material use by 34% 9.
Waste-to-Value Conversion: AI-powered sorting diverts 95%+ of metals from landfills, as seen in Kuljetusrinki’s facility, which repurposed 6,900+ tons/year of scrap using ZenRobotics 48.
Policy Compliance: AI ensures adherence to regulations like China’s Green Fence by delivering contamination-free batches, increasing resale value by 25% 19.
Implementation Roadmap & Vendor Evaluation Tips
Step 1: Assess Facility Needs
Audit current sorting efficiency, labor costs, and contamination rates.
Prioritize goals: purity improvement, throughput, or labor safety 110.
Step 2: Vendor Selection Criteria
ZenRobotics: Heavy-duty sorting, compliance-focused – ROI in 12–18 months
AMP Robotics: High-speed picking, cloud-based analytics – ROI in 6–12 months
EverestLabs: Modular systems, small-scale adaptability – ROI in 12–18 months
Recycleye: Retrofittable vision systems, low upfront cost – ROI in 18–24 months
Step 3: Pilot Testing
Run trials with vendors like Glacier (90% detection accuracy) or Integrated Recycling Technologies (75+ circuit board classifications) to validate performance 1.
Use feedback loops to refine AI models for site-specific waste streams 6.
Step 4: Workforce Transition
Upskill workers into AI supervisors and maintenance technicians. For example, Skrotfrag reduced manual labor by 40% while creating higher-skilled roles 89.
Step 5: Full-Scale Deployment
Integrate AI with IoT sensors for real-time monitoring (e.g., Tecnoap’s SCRAPYARD) 1.
Leverage predictive maintenance to reduce downtime by 30% 9.
Future-Forward Insights
AI-Powered Circular Hubs: By 2030, smart MRFs will combine robotics, blockchain for material tracing, and AI-driven carbon accounting to meet net-zero targets 213.
Policy-Driven Adoption: Stricter EU regulations (e.g., Carbon Border Adjustment Mechanism) will mandate AI adoption for emissions reporting and material purity 9.
Next-Gen AI: Advances in quantum computing and generative AI will enable real-time multilingual waste analysis and self-optimizing sorting lines 6.
Conclusion
The fusion of AI and robotics is not just transforming scrap metal sorting—it’s redefining the circular economy. From ZenRobotics’ precision to AMP’s speed, these technologies are unlocking unprecedented efficiency and sustainability. As facilities adopt tailored solutions, the industry will shift from linear waste chains to closed-loop systems, where every scrap metal particle is a resource, not rubbish.
Ready to implement AI? Start with a pilot, choose vendors aligned with your KPIs, and prepare your workforce for the automation revolution. The future of recycling is intelligent, adaptive, and inevitable.
For further details, explore case studies from ZenRobotics and AMP Robotics.