How to Audit Your Scrap Metal Supply Chain for Maximum Transparency
Learn how to audit your scrap metal supply chain for maximum transparency. Discover actionable steps to ensure ethical sourcing, prevent fraud, and stay compliant with regulations while enhancing sustainability and brand credibility.
SUSTAINABLE METALS & RECYCLING INNOVATIONS
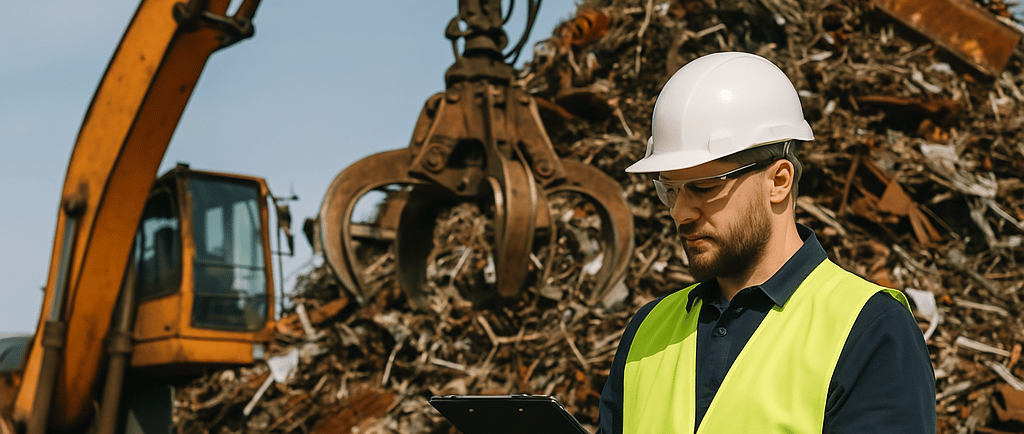
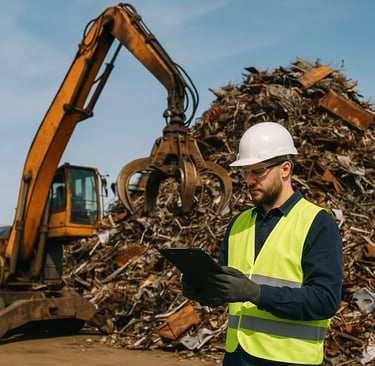
In today’s business landscape, sustainability and accountability aren't just buzzwords—they’re bottom-line essentials. Particularly in the $500 billion global scrap metal industry, where environmental and ethical concerns loom large, implementing a transparent, ethically sound supply chain can dramatically boost your brand’s credibility and sustainability metrics.
Whether you're a recycling company, a manufacturer sourcing raw material, or a scrap dealer, successfully auditing your scrap metal supply chain requires a structured approach to ensure ethical sourcing, prevent fraud, and stay compliant with recycling regulations.
According to the Institute of Scrap Recycling Industries (ISRI), over 130 million metric tons of recyclable metal are generated annually. With the increasing demand for circular economy models and ESG (Environmental, Social, Governance) transparency from institutional investors, auditing your scrap metal operations isn’t just responsible—it’s strategic.
In this guide, we’ll walk you through how to conduct a thorough scrap audit, vet your suppliers for ethical operations, and embed transparency across your entire scrap metal supply chain.
Why Scrap Metal Supply Chain Transparency Matters
Before diving into the how, let’s take a strategic look at the why. Scrap metal is essential to building a sustainable industrial ecosystem. It supports circular economies, reduces carbon footprints, and decreases demand for virgin ore extraction — a process that contributes substantially to deforestation, water contamination, and greenhouse gas emissions.
The Cost of a Non-Transparent Supply Chain
Lack of visibility in the scrap supply chain can lead to broader risks beyond regulatory violations. Forbes recently reported that supply chain fraud costs U.S. companies an estimated $140 billion annually. In the scrap sector, non-transparency isn't just a logistical issue—it’s a reputational landmine.
Common Risks Include:
Illegal sourcing: The use of stolen or conflict metal can lead to criminal investigations, embargoes, and legal penalties.
Environmental violations: Improper processing or unregulated dumping of scrap can cause site shutdowns and significant fines.
Human rights abuses: Poor labor practices, including underage labor in offshore facilities, can severely harm brand equity.
Financial fraud: From falsified weight tickets to misclassified scrap grade, these manipulations distort pricing and compliance tracking.
A notable case illustrating these risks is the 2018 crackdown on illegal electronic scrap exports from the U.S. to Asia, which resulted in multiple businesses receiving fines exceeding $1 million.
Building transparency into your scrap metal chain is more than a compliance tactic—it’s a business imperative.
Step 1: Map Your Entire Scrap Metal Supply Chain
Transparency starts with visibility. To manage your risks, gains, and growth expectations, you need a granular understanding of your entire supply network.
Identify All Stakeholders
Start by compiling a comprehensive inventory of every stakeholder touching your scrap stream:
Material collectors (independent scrappers, MRFs—material recovery facilities)
Brokers and middle-market aggregators
Transporters and freight companies
Local, regional, or international recyclers, smelters, and processors
End-buyers, particularly in vertical manufacturing chains
Every node in your value chain introduces its own risk posture. Some suppliers might engage in sourcing from unregulated regions, while others may lack precise material tracking capabilities.
Visualize the Flow of Material
Use visual planning tools to illustrate how scrap travels through your network. This includes:
Point of origin
Modes of transport and storage centers
Processing points (sorting, shredding, smelting)
Final use (metal fabrication or resale market)
Tools for Mapping and Analysis:
Sourcemap: Widely used by companies like Ferrero and Mars to map suppliers and assess ethical risks.
Resilinc: Monitors suppliers for geopolitical, environmental, and financial risks in real-time.
SupplyShift: Allows customizable supplier scorecards built around ethical parameters.
Even spreadsheets or flowcharts drawn via tools like Miro or Lucidchart can shed light on weak points where transparency breaks down.
Mapping is the foundation upon which you’ll layer deeper audits and performance benchmarks.
Step 2: Evaluate Supplier Credentials and Certifications
As oversight increases, suppliers without robust governance practices can expose your business to risks that range from compliance gaps to consumer boycotts.
Red Flags in Supplier Documentation
When reviewing supplier credentials, go beyond just checking expiration dates. Spot inconsistencies such as:
Discrepancies between license registration addresses and facility locations.
Absence of third-party audits for required certifications.
Irregularities in ISO audit schedules.
Industry-Recognized Certifications to Look For:
ISO 14001 (Environmental Management System): Demonstrates commitment to sustaining environmental performance.
ISO 9001 (Quality Management System): Ensures consistent product and service quality.
R2v3 Certification: For responsible recyclers, especially dealing with e-waste.
e-Stewards: Endorsed by the Basel Action Network; focuses on ethical disposal of electronics.
Cross-reference any shared certifications against public databases such as the International Accreditation Forum or certification bodies like SGS and UL.
ESG Reports as Transparency Indicators
While less standardized than ISO certifications, ESG reports offer crucial insight into a supplier’s ethics. These reports often cover:
Carbon emissions tracking
Community engagement efforts
Internal diversity programs
Governance and anti-corruption practices
Pro Tip: When a supplier lacks an ESG report, initiate an ESG questionnaire to gauge where they stand on key metrics.
Step 3: Conduct an On-Site Scrap Audit (or Virtual Alternative)
While digital records and certifications provide a paper trail, an on-site audit uncovers the truth beneath the documentation.
Key Audit Areas
Material Handling: Look for contamination, mixing of scrap grades, and unsafe storage.
Scale Calibration Logs: An uncalibrated scale offers an easy avenue for transactional fraud.
Employee Safety: OSHA compliance, PPE usage, and fair shift practices must be verified in person.
Environmental Controls: Check for water filtration, air quality monitoring systems, and spill containment procedures.
A 2021 audit by Apple’s Environment and Supply Chain Innovation team discovered more than 225 supplier code violations, including failing to contain hazardous substances near local communities. This serves as a powerful reminder of onsite audits’ importance.
Virtual Audit Tactics
When site visits are impossible:
Request date-stamped and geo-tagged walkthrough videos.
Use platforms like iAuditor for remote inspections.
Conduct live Skype/Zoom audits with interactive Q&A sessions.
Analyze updated Google Earth imagery for external condition audits.
Combine visual data with documentation to create layered validation.
Step 4: Implement a Supplier Scorecard System
Data without structure is just noise. That’s where scorecards come in — enabling quantitative risk profiling and consistent comparison over time.
Core Criteria to Track
Certification Validity and Breadth
Environmental Audit Scores
Labor Practice Ratings (e.g., fair wage compliance, welfare facilities)
Reputation Scores (peer reviews, past violations)
Supply Reliability Metrics (on-time delivery, dispute frequency)
Assign weighted scores based on your business objectives. For example:
A green-certified tech company may assign a 40% score weight to emissions control.
A firm working with public contracts might prioritize anti-fraud controls.
Case Study: Benchmarking Suppliers with Scorecards
Toyota’s North American scrap program saw a 12% improvement in material traceability and a 9% reduction in regulatory issues after adopting a supplier rating index across their scrap vendors.
Just as marketing uses KPIs to refine campaigns, your scorecard acts as a performance ROI dashboard for supplier ethics.
Step 5: Leverage Technology for Real-Time Tracking and Traceability
Modern supply chains demand modern solutions. Integrating advanced technologies into your scrap metal operations can bridge gaps in visibility and ensure end-to-end accountability.
Blockchain for Immutable Records
Blockchain technology creates tamper-proof ledgers of transactions, making it ideal for tracking scrap metal from source to final buyer. For example, IBM’s Blockchain Transparent Supply platform allows companies like Ford to trace conflict-free minerals, ensuring ethical sourcing. By recording each transfer of custody, weight, and processing step on a blockchain, you eliminate opportunities for fraud or misrepresentation.
IoT Sensors and RFID Tags
Embedding IoT sensors or RFID tags in scrap shipments enables real-time monitoring of location, temperature, and handling conditions. Companies like ArcelorMittal use IoT-enabled bins to track scrap metal quality and contamination levels during transit, reducing disputes over material integrity.
Digital Material Passports
These digital profiles document a scrap batch’s origin, composition, and processing history. Platforms like Circulor integrate AI to analyze data from material passports, flagging anomalies such as unexpected stops or deviations from declared routes.
Case Study: Rio Tinto’s Mine-to-Metal Initiative
Rio Tinto partnered with SAP to deploy a blockchain-based system across its aluminum supply chain. The platform reduced administrative costs by 30% and increased traceability compliance by 90%, showcasing how tech-driven transparency can yield financial and operational benefits.
Step 6: Establish a Continuous Monitoring and Improvement Process
Audits are not one-time events. To maintain transparency, implement systems for ongoing oversight and adaptive risk management.
Automated Compliance Alerts
Use tools like EcoVadis or Assent Compliance to monitor regulatory changes (e.g., updates to Basel Convention guidelines) and automatically alert suppliers to new requirements. This proactive approach minimizes compliance lag and fosters collaboration.
Corrective Action Plans (CAPs)
When audits uncover issues, work with suppliers to develop CAPs with clear timelines. For instance, a smelter failing emissions tests might commit to installing filters within six months. Track progress via shared dashboards like those offered by Achilles ESG.
Supplier Training Programs
Educate vendors on emerging standards through workshops or e-learning platforms. The Responsible Business Alliance offers free courses on ethical sourcing and environmental management, empowering suppliers to self-correct.
Third-Party Whistleblower Platforms
Tools like EthicsPoint allow anonymous reporting of fraud or safety violations, creating a culture of accountability. GM’s supply chain saw a 20% drop in violations after implementing such a system.
Step 7: Engage Stakeholders and Communicate Transparency Efforts
Transparency loses value if it isn’t shared. Build trust by openly communicating your supply chain integrity to investors, customers, and regulators.
Publish Annual Transparency Reports
Detail audit findings, corrective actions, and ESG milestones in publicly accessible reports. Tesla’s Impact Report, for example, highlights recycled material usage in batteries, reinforcing its commitment to circular economies.
Collaborate with Industry Alliances
Join initiatives like the Global Recycling Standard or the Aluminum Stewardship Initiative to align with best practices and gain third-party verification. Participation signals credibility and attracts ESG-focused investors.
Customer-Facing Traceability Tools
Consider QR codes on products linked to sourcing data. Audi’s “Aluminum Closed Loop” program lets customers scan a code to see the recycled content’s journey, enhancing brand loyalty.
Conclusion: Building a Sustainable Future Through Transparent Supply Chains
Auditing your scrap metal supply chain is not merely a compliance exercise—it’s a strategic lever for growth. By mapping stakeholders, vetting suppliers, deploying technology, and fostering a culture of continuous improvement, you mitigate risks while positioning your brand as a leader in the circular economy.
The scrap industry’s role in decarbonizing manufacturing cannot be overstated. With global demand for recycled metals projected to grow 8% annually (McKinsey, 2023), businesses that prioritize transparency today will dominate the sustainable markets of tomorrow.
Your Move
Start small: Pick one link in your supply chain to audit this quarter. Use the tools and frameworks outlined here to build momentum. Remember, transparency is a journey—and every step forward strengthens your business, your industry, and the planet.