Metal Recycling Technologies Explained: From Shredders to AI-Powered Sorting
Explore cutting-edge technologies revolutionizing metal recycling—from industrial shredders to AI-powered sorting systems. Discover how sensor-based identification, robotics, and machine learning are driving efficiency, reducing emissions, and advancing the circular economy. Learn how these innovations conserve energy, recover high-purity metals, and position the $140B+ scrap industry for a sustainable future
SUSTAINABLE METALS & RECYCLING INNOVATIONS
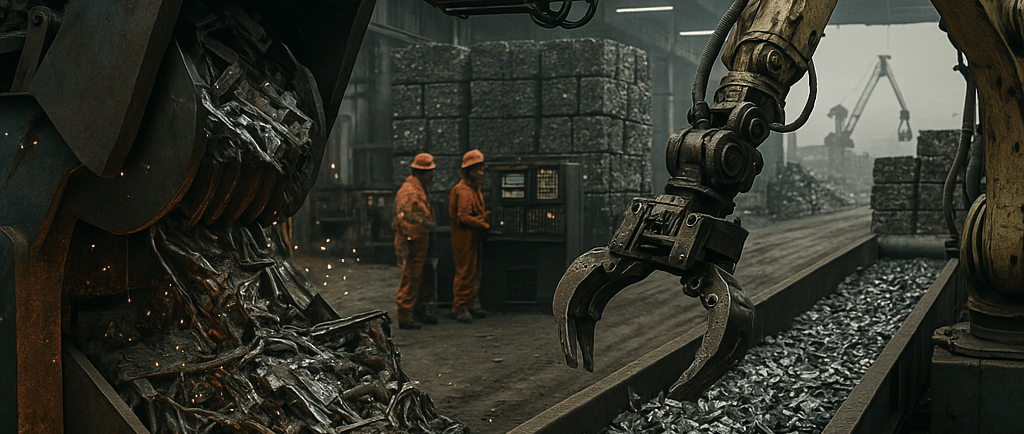
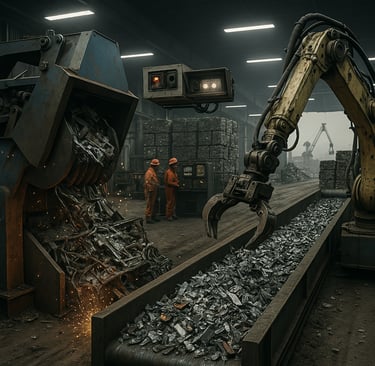
Introduction
The global demand for sustainable resource utilization has reached a critical inflection point. As industries intensify their commitment to environmental sustainability, and as consumers become more educated about their ecological footprint, metal recycling has become a cornerstone of smarter, greener production systems. This evolution isn’t just about reducing waste; it’s about completely reimagining how we recover and repurpose metals in a circular economy.
At the core of these transformations are innovative metal recycling technologies that offer unprecedented efficiency, precision, and environmental impact mitigation. From high-torque shredders to intelligent AI-guided sorters, the metal recycling industry now harnesses the power of automation, data science, and material science. The result? Scalable systems capable of processing thousands of tons of scrap metal per day with minimal waste and maximum recovery.
This guide dives deep into the technological advancements propelling modern recycling—from physical breakdown of scrap to the smart machines that analyze, sort, and elevate recycled metals to near-pure states. Whether you’re an environmental engineer, a waste management executive, or just a curious reader, this breakdown offers clarity on how leading-edge innovation is influencing the trajectory of metal reuse.
The Value of Metal Recycling in the Circular Economy
Before exploring how recycling technologies operate, it’s crucial to understand their significance within the circular economy—a regenerative economic model designed to eliminate waste and keep resources in use for as long as possible.
Why Recycling Metals Is Crucial
Metals such as aluminum, copper, steel, and zinc are pivotal for industries ranging from construction to electronics. Despite their utility, mining these materials from the earth is highly energy-intensive and environmentally damaging. For example, the process of mining and refining bauxite ore into aluminum releases significant carbon dioxide (CO₂) emissions and consumes large volumes of water and electricity.
Recycling circumvents these challenges. According to data from the Aluminum Association:
Recycling aluminum conserves up to 95% of the energy needed to produce new aluminum from ore.
Steel recycling saves approximately 60–74% of energy compared to producing virgin steel.
For copper, the energy saving is around 85%, underscoring its immense benefit in the electronics and wiring sectors.
This remarkable efficiency aligns tightly with United Nations Sustainable Development Goals (SDGs), particularly goals 9 (Industry, Innovation, and Infrastructure), 12 (Responsible Consumption and Production), and 13 (Climate Action).
How Metal Recycling Integrates in Circular Systems
The essence of the circular economy is maintaining the value of products, materials, and resources in the economy for as long as possible while minimizing resource extraction and waste generation.
Thus, by extending the lifecycle of metals through recycling, industries can:
Dramatically reduce landfill dependency
Improve raw material security and independence
Shrink greenhouse gas (GHG) emissions across the supply chain
Stimulate green job creation in recycling and remanufacturing sectors
In 2022, the global scrap metal recycling market was valued at over 70 billion and is projected to surpass 140 billion by 2032, according to a report by ResearchAndMarkets. These figures reflect both economic promise and environmental necessity.
Overview of Modern Recycling Technology
The days of manually sorting through scrap heaps are long gone. Today, modern recycling systems are sophisticated, interconnected, and frequently powered by artificial intelligence, IoT (Internet of Things), robotics, and data analytics.
Strategic Goals Driving Technological Advances
The primary objectives that modern recycling technology seeks to achieve include:
Maximizing metal yield: Especially critical as virgin materials become scarcer and more expensive.
Ensuring material purity: High-purity outputs are suitable for industrial applications and reduce secondary refining stages.
Automating repetitive tasks: Helps solve labor shortages and improves worker safety by reducing human interaction with hazardous materials.
Lowering environmental impact: Technologies are aimed at reducing CO₂ emissions, noise pollution, and energy usage inherent in older processes.
These processes are proving vital for Materials Recovery Facilities (MRFs) and Specialty Metal Refiners, where speed and precision are critical for profitability and compliance.
How Technology Integrates at Scale
End-to-end metal recycling operations often incorporate multiple overlapping technologies to handle variables like material composition, contamination levels, and throughput requirements. A modern facility typically operates in the following steps:
Initial intake and auditing
Primary shredding and liberation
Magnetic and eddy current separation
Sensor-based material identification
Robotic or AI-based sorting
Material compaction or baling for redistribution
This integrated approach ensures not only heightened efficiency but also increased traceability across every stage of the recycling process.
1. Mechanical Methods: The Foundation of Metal Recycling
Mechanical processing still forms the backbone of many metal recycling operations. It provides the raw throughput and initial stages of material liberation that enable downstream technologies to function efficiently.
Shredders: Breaking Down the Bulk
Industrial shredders have evolved dramatically from their early iterations. Today’s designs emphasize energy efficiency, durability, and adaptability to different feedstocks.
Types of Industrial Shredders in Detail:
Hammermill Shredders: These are typically used for auto scrap and appliances. Their rapidly spinning hammers crush metal against anvils to break it into smaller parts.
Twin-Shaft Shear Shredders: Due to their low-speed, high-torque output, these are ideal for bulky materials like steel beams, white goods, and engine blocks.
Granulators and Ring Mills: Used for lighter metals and applications requiring tightly confined output sizes, such as aluminum foil or beverage cans.
For example, global manufacturer Metso Outotec offers heavy-duty shredders capable of processing 80+ tons of ferrous scrap per hour. These machines also come equipped with load monitoring systems and energy optimization modules, helping facilities reduce their operational carbon footprint.
Magnetic Separation & Eddy Current Systems: Primary Sorting Mechanisms
Once shredded, materials flow along conveyor systems where they undergo initial separation.
Magnetic Separators: Typically utilize rare-earth magnets for powerful, efficient separation of ferrous metals. Many setups now include self-cleaning mechanisms and variable-speed belts to optimize performance.
Eddy Current Separators: Use magnetic rotors to create alternating electric fields. Non-ferrous metals like aluminum and brass are repelled, effectively sorting them from other fractions.
These systems are fast, automated, and robust—capable of sorting hundreds of tons of mixed materials daily. The result is a significant concentration of homogenous metal types, preparing the batch for more specific identification and reclaiming steps.
2. Sensor-Based Sorting: Precision in Material Identification
Sensor-based sorting represents a quantum leap in recycling accuracy, enabling facilities to achieve material purities exceeding 95% by leveraging advanced detection technologies. These systems analyze physical and chemical properties of materials in real time, such as density, conductivity, and spectral signatures, to separate metals and contaminants with surgical precision.
Key Technologies and Applications
Induction Sensors: Detect conductive metals (e.g., copper, aluminum) by measuring electromagnetic responses. MSS MetalMiner systems, for instance, recover residual metals from e-waste with minimal loss.
X-ray Transmission (XRT): Identifies materials based on atomic density. Tomra’s X-TRACT units isolate high-purity aluminum by ejecting heavy metals like magnesium.
Near-Infrared (NIR) Spectroscopy: Sorts plastics by resin type but struggles with black plastics due to carbon absorption. STEINERT’s UniSort systems combine NIR with laser spectroscopy to overcome this limitation.
AI-Enhanced Optical Sorters: Combine cameras and machine learning to recognize shapes, colors, and textures. ZenRobotics’ Heavy Picker uses this to distinguish copper "meatballs" from ferrous scrap, achieving <0.1% copper contamination in steel streams.
Case Study:
A European e-scrap facility integrated Tomra’s COMBISENSE and FINDER units, boosting copper recovery by 30% while reducing plastic contamination. By preprocessing with shredders and eddy currents, the system achieved 98% metal purity.
Challenges:
Black plastics remain problematic due to filler variability, though laser-based sorters and electrostatic separators are emerging solutions.
3. Robotics: Automating Hazardous and Complex Tasks
Robotic systems are transforming recycling workflows by handling dangerous, repetitive, or precision-dependent tasks. Equipped with AI and advanced grippers, these robots excel in environments where human labor is unsafe or inefficient.
Innovations in Robotic Recycling
Heavy-Duty Sorting: ZenRobotics’ Heavy Picker uses three robotic arms to sort metals like stainless steel and zinc at 4,000 picks/hour, reducing labor costs by 50%.
Scrap Cutting: WPI’s autonomous framework employs active vision systems to plan cutting paths for large scrap (e.g., ships), improving speed and safety compared to manual torch cutting.
Adaptive Learning: Robots like those from ZenRobotics train on thousands of material samples, refining their ability to identify rare metals (e.g., indium in LCD screens).
ROI:
Facilities report payback periods of 12–18 months due to efficiency gains and reduced downtime.
4. AI and Machine Learning: The Brain Behind Smart Recycling
AI integrates sensor data, historical patterns, and predictive analytics to optimize every recycling stage—from intake to final sorting.
AI-Driven Advancements
Real-Time Optimization: ZenBrain (ZenRobotics’ AI) adjusts sorting parameters dynamically based on feed composition, improving recovery rates by 15–25%.
Predictive Maintenance: AI models monitor equipment health, predicting failures in shredders or conveyors before they occur, reducing downtime by up to 30%.
Quality Control: XRF analyzers paired with AI validate metal purity, ensuring compliance with standards like ASTM for recycled aluminum.
Case Study:
A U.S. steel mill reduced copper contamination to 0.08% using AI sorters, avoiding $1.2M/year in penalties for non-compliant batches.
5. Future Innovations: Toward Autonomous Recycling Ecosystems
The next frontier involves fully integrated, self-optimizing systems powered by IoT, blockchain, and advanced material science.
Emerging Trends
Multi-Sensor Fusion: STEINERT’s KSS combines XRT, NIR, and 3D imaging to sort complex streams (e.g., shredded electronics) in a single pass.
Hydrogen-Powered Shredders: Trials in Europe show 40% lower carbon emissions compared to diesel models.
Circular Supply Chains: Blockchain platforms track recycled metals from scrap to product, enhancing traceability for automakers and builders.
Bioleaching: Using bacteria to extract precious metals from low-grade e-waste, potentially recovering 99% of gold from PCBs.
Prediction:
By 2030, 70% of recycling facilities will deploy AI-driven systems, cutting global CO₂ emissions by 150 million metric tons annually.
Conclusion
From sensor-based sorters that identify metals at molecular levels to AI robots that learn on the job, these technologies are redefining metal recycling’s role in the circular economy. As innovations converge—think hydrogen energy, blockchain, and bioleaching—the industry is poised to achieve near-zero waste and energy-neutral operations. For stakeholders, investing in these systems isn’t just environmentally prudent; it’s a strategic imperative to lead in the $140B+ scrap market of tomorrow.