Predictive Analytics: Forecasting Scrap Metal Supply and Demand
Discover how predictive analytics revolutionizes scrap metal supply chains: master demand forecasting, optimize inventory, reduce costs & future-proof your recycling business with AI/ML.
AI & DIGITAL ENGAGEMENT IN SUSTAINABILITY
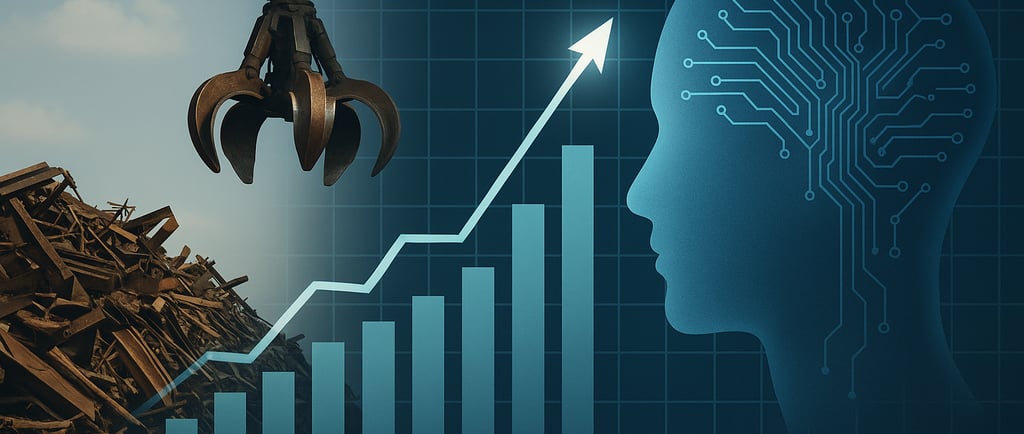
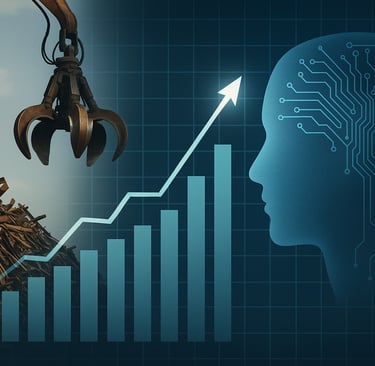
In today’s fast-paced manufacturing and recycling environments, the dynamics of the scrap metal market have become increasingly complex. Volatility in commodity prices, inconsistent supply chains, and evolving environmental regulations all contribute to an unpredictable and fragmented ecosystem. For businesses operating within the scrap metal supply chain—from recyclers and smelters to manufacturers and distribution networks—navigating these market fluctuations isn’t just a challenge, it’s make-or-break for their bottom line.
Global shifts in industrial production, seasonality in recycling patterns, and sudden regulatory changes can quickly disrupt operations. Businesses need the capacity not only to respond but to anticipate what comes next. That’s why many industry leaders are turning to advanced analytics.
Enter predictive analytics: the data-driven superpower that’s transforming how organizations forecast scrap metal supply and demand, optimize inventory management, and build resilience into their operations. With the increasing adoption of artificial intelligence (AI) and machine learning (ML), predictive analytics is becoming a standard operational tool rather than a novel advantage.
In this article, we explore how predictive analytics is reshaping the scrap metal industry—from smarter demand forecasting and precision inventory control to supply stabilization and strategic adaptability.
What is Predictive Analytics?
Predictive analytics refers to a category of advanced data analytics that leverages historical data, statistical techniques, machine learning algorithms, and even deep learning to predict future outcomes. It moves beyond descriptive analytics ("What happened?") and diagnostic analytics ("Why did it happen?") to provide predictions on "What is likely to happen next?" based on patterns and trends in data.
In the scrap metal industry, where uncertainty is the norm, predictive analytics unlocks powerful use cases. Organizations can analyze immense volumes of structured and unstructured data—from global commodity markets to local recycling behaviors—to make data-driven decisions in near real-time.
How It Works:
Predictive models crunch input variables, such as:
Commodity futures (e.g., copper, steel, aluminum)
Input and output from material recovery facilities (MRFs)
Macro indicators such as GDP growth, industrial output, and automotive sales
Regional recycling data, urban infrastructure development, and transportation patterns
These inputs are processed through machine learning algorithms that recognize historical patterns and generate forecasts with increasing accuracy over time. Machine learning models refine themselves as more data becomes available—an essential capability in a highly dynamic and data-rich environment like scrap metal.
Key Technologies:
Regression Models
Neural Networks
Time-Series Forecasting
Decision Trees
Natural Language Processing (in unstructured document mining)
The convergence of data availability, cloud computing, and scalable analytics tools has made predictive analytics much more accessible—even for mid-sized firms without a large internal data science team.
The Unique Challenges of the Scrap Metal Supply Chain
To appreciate the value of predictive analytics, it’s essential to understand the complex challenges that plague the scrap metal industry.
1. Volatile Pricing
Global scrap metal prices are heavily influenced by fluctuating demand in emerging economies, tariffs on imported goods, and macroeconomic conditions.
For instance, according to the World Bank, non-ferrous metals saw a price surge of over 20% in 2021 due to supply-chain disruptions and resurgent post-pandemic demand. Similarly, the Russia-Ukraine conflict led to a significant shift in steel prices, affecting procurement strategies globally.
Such volatility makes setting pricing strategies difficult, especially for procurement officers who must decide when to buy or hold based on predicted price trends.
2. Irregular Supply
Unlike traditional mining operations where raw material output is relatively predictable, scrap metal depends on collection rates, consumer recycling habits, and industrial decommissioning timelines. This supply is inherently non-linear and is often influenced by local behaviors and unpredictable events such as demolition projects or rapid fleet upgrades.
3. Regulatory Impact
Legislative actions—like China's National Sword policy in 2018, which limited importation of certain scrap materials—can instantly reshape global scrap flows. More recently, the EU’s Green Deal and sustainability targets aim to enhance circular economic adoption, affecting how scrap material is processed and what markets remain accessible.
4. Geographical Disparities
Regional differences in infrastructure, proximity to recycling centers, and access to ports affect transportation costs and availability. For example, recycling rates in metropolitan areas may far exceed those in rural regions due to accessibility, creating logistical bottlenecks or surpluses in supply.
Navigating these intricacies requires accurate foresight. Gut instinct and experience—while valuable—fall short when data can illuminate what’s coming with far more precision.
Predictive Analytics in Action: Demand Forecasting in the Scrap Market
Accurately forecasting scrap metal demand can significantly improve decision-making in everything from procurement to production planning and customer contract negotiations.
Understanding Demand Drivers
Predictive demand models examine leading indicators such as:
Construction Permits: An increase in real estate development signals rising demand for steel and aluminum.
Auto Industry Cycles: The global automotive industry's scrap usage accounts for a sizeable share—over 25% in developed markets—for aluminum and stainless steel.
Regulatory Initiatives: For example, India's Vehicle Scrappage Policy (2021) encourages demolition of old vehicles, increasing demand for recycled metals.
Consumer Electronics Growth: With electronics recycling becoming more prevalent, metals like gold, palladium, and platinum tied to devices offer new demand patterns.
ML models can digest dozens of these variables simultaneously across different time horizons. Over the last few years, companies who adopted such systems have seen forecast error reduction of up to 35%, resulting in more reliable supply contracts and optimized asset usage.
Real-Time Adjustments
The scrap marketplace moves quickly. Real-time predictive analytics systems offer up-to-the-minute refinement of forecasts. One major European scrap processor uses streaming data from commodity exchanges, manufacturing partners, and sensor-equipped bins to update its projections every hour.
By adapting in real-time, businesses can dynamically price their materials, adjust delivery timelines, or even re-route shipments to higher-demand regions.
Business Benefits
Here’s how predictive demand forecasting creates meaningful business impact:
✔ Increased Sales Accuracy: Forecasting powered by AI helps businesses avoid missed sales due to stockouts or delayed sourcing.
✔ Customer Trust and Retention: Manufacturers are more likely to work with suppliers who consistently meet delivery metrics.
✔ Higher Profit Margins: Anticipating demand swings allows companies to adjust pricing ahead of competitors.
As predictive analytics matures, forward-looking demand forecasts become a strategic asset. Organizations that combine analytics with agile execution can capture new market opportunities before others recognize them.
Forecasting Scrap Metal Supply: Turning Chaos into Clarity
Understanding where supply will come from—and when—is often more difficult than predicting demand. Yet with the right analytics, even this moving target becomes manageable.
Data-Driven Supply Modeling
Supply forecasting requires visibility into the origin points of scrap. Input variables include:
Product Retirement Cycles: Knowing when fleets, electronics, or infrastructure reach end-of-life helps predict future scrap input volumes.
Local Demolition Trends: City planning records and permits for demolition offer a forward-looking view into potential metal surges.
Industrial Output Declines: A dip in manufacturing may signal increased obsolescence and disposal of machinery.
For example, if predictive models detect a spike in commercial real estate demolition in the US Midwest, processing facilities can proactively schedule additional labor and sorting capacity.
Edge Computing and IoT Integration
Smart scrapyards now employ edge technologies and IoT devices, such as RFID-tagged bins and automated sorting machines, to monitor inflow rates, contamination levels, and material weights. This real-time data feeds into cloud-based analytics systems.
Scrap processing facilities using IoT have reported a 20–30% improvement in material classification accuracy and 18% decrease in operational waste within the first 12 months.
Benefits of Predictive Scrap Supply Forecasting
Effectively managing supply through predictive insights translates to:
🚚 Reduced Transport and Logistical Disruptions: Preempt delays caused by regional supply constraints.
📈 Improved Procurement Strategies: Know when to pre-purchase contracts or delay sourcing to capitalize on input trends.
💼 Operational Efficiency: Predict volume fluctuations for appropriate labor scheduling, improving throughput without overtime costs.
By turning reactive planning into proactive strategy, predictive analytics positions recycling organizations to maintain profitability—even during market downturns or seasonal shortages.
Deep Dive into Predictive Analytics for Scrap Metal
Building on the foundation laid in the blog, let's explore the crucial areas it touched upon but didn't fully develop: strategic inventory management, real-world proof, actionable implementation, and the future landscape.
1. Strategic Inventory Management: The Predictive Edge
Predictive analytics transforms inventory from a cost center to a strategic asset by enabling dynamic optimization based on anticipated supply and demand. Here's how it goes beyond basic forecasting:
Dynamic Safety Stock Calculation: Instead of static safety stock levels based on historical averages, ML models continuously calculate optimal safety stock by location and material type using predicted supply volatility, forecasted demand uncertainty, lead times, and desired service levels. This minimizes both stockouts and excess capital tied up in inventory.
Optimal Replenishment Timing & Quantity: Predictive models integrate supply forecasts (e.g., expected scrap inflow from a major demolition project next month) and demand forecasts to determine the precise timing and quantity for purchasing or transferring materials. This prevents overbuying during anticipated supply surges or under-buying before predicted demand spikes.
Network Optimization: For businesses with multiple yards or processing facilities, predictive analytics helps determine the most cost-effective flow of materials between locations. Should surplus Aluminum from Yard A be shipped to Yard B anticipating higher demand there, or held? Models optimize based on transportation costs, processing capacity forecasts, and local demand predictions.
Condition-Based Grading & Pricing Integration: Predictive models can incorporate expected quality/grade based on source data (e.g., IoT sensor data from bins, origin of scrap). This allows for more precise inventory valuation and dynamic pricing strategies linked to predicted market value for that specific grade at the time it's expected to be sold.
Reducing Obsolescence & Holding Costs: By accurately predicting shifts in material demand (e.g., decline in demand for a specific alloy), businesses can proactively liquidate stock before it becomes obsolete or negotiate contracts to move it, significantly reducing holding costs and write-downs.
2. Real-World Case Studies: Industry Leaders Leveraging Prediction
Case Study 1: Global Recycler Reduces Stockouts by 40%
Challenge: A major international metal recycler faced frequent stockouts of high-demand stainless steel grades, damaging customer relationships and missing sales opportunities.
Solution: Implemented an ML-based demand forecasting system incorporating real-time data from manufacturing partners, commodity indices, and regional economic indicators. Integrated forecasts directly into their inventory replenishment system.
Result: Achieved a 40% reduction in stockouts within 18 months, leading to significantly improved customer satisfaction scores and an estimated 8% increase in sales revenue for those grades due to reliable availability.
Case Study 2: Regional Processor Optimizes Logistics & Labor
Challenge: A mid-sized scrap processor struggled with inefficient truck routing (empty miles) and unpredictable labor needs due to volatile scrap inflows from municipal and industrial sources.
Solution: Deployed IoT sensors at collection points and partnered with municipalities for access to demolition permit data. Used time-series forecasting to predict daily/weekly scrap inflow volumes and types by location. Integrated forecasts with logistics and workforce management software.
Result: Reduced transportation costs by 15% through optimized routing based on predicted pickup volumes. Improved labor scheduling accuracy by 25%, reducing overtime costs by 20% and increasing yard throughput.
Case Study 3: Smelter Mitigates Price Volatility Impact
Challenge: A non-ferrous smelter was highly exposed to volatile copper scrap prices, making procurement decisions risky and impacting margins.
Solution: Developed a predictive pricing model combining historical price data, futures curves, global supply/demand indicators (e.g., mine output, manufacturing PMIs), and proprietary scrap supply forecasts. Used the model to inform forward purchasing contracts and timing of spot market buys.
Result: Reduced average procurement costs by 5% compared to previous methods, significantly improving margin stability despite ongoing market volatility. Enhanced ability to offer more competitive, yet profitable, pricing to customers.
3. Actionable Steps to Start Implementing Predictive Analytics
Getting started doesn't require a massive budget or PhD data scientists on day one. Follow this phased approach:
Define Clear Objectives & KPIs: Start small. What's the one biggest pain point? (e.g., "Reduce forecast error for #1 Copper by 20%," "Cut safety stock costs for Aluminum by 15%"). Define measurable KPIs.
Audit & Consolidate Your Data: Identify available data sources (ERP, scale tickets, IoT sensors, commodity feeds, public data like permits/GDP). Assess quality (completeness, accuracy). Prioritize integrating core operational data first.
Start Simple (Descriptive/Diagnostic): Before predicting the future, understand the past/present. Use basic BI tools to visualize trends, identify correlations (e.g., between local construction starts and shredded steel demand). Cleanse data during this phase.
Pilot a Focused Project: Choose one specific, high-impact use case (e.g., forecasting demand for your top 3 customers, predicting inflow from your largest municipal contract). Leverage cloud-based analytics platforms (e.g., AWS SageMaker, Azure ML, Google Vertex AI) that offer pre-built algorithms and require less coding expertise.
Leverage Expertise (Internal/External): Upskill an internal analyst or partner with a specialized analytics consultancy or solution provider familiar with commodities/recycling. Don't try to build everything from scratch internally initially.
Build the Model & Integrate: Develop the predictive model using relevant historical data. Focus on interpretability. Integrate the model's output (forecasts, recommendations) into existing workflows – this is crucial! (e.g., feed demand forecasts into the procurement system, show predicted inflows on the yard manager's dashboard).
Monitor, Refine, and Scale: Track model performance against your KPIs. Continuously feed new data to retrain and improve the model. Start small, prove value, then expand to other materials, processes, or locations.
4. Outlook: The Data-Driven Future of Scrap Metal
Predictive analytics is just the foundation. The future is shaped by the convergence of advanced data intelligence technologies:
Hyper-Personalized Supply Chains: AI will enable dynamic, micro-segmented pricing and service offerings based on predicted customer needs and real-time market conditions.
Closed-Loop Systems Integration: Predictive models will seamlessly integrate with product design data (from manufacturers) and advanced recycling technologies, optimizing the flow of specific alloys back into production with minimal downgrading.
AI-Driven Trading & Risk Management: Sophisticated AI agents will autonomously execute trades, hedge positions, and manage procurement/sales portfolios in real-time based on predictive signals, far surpassing human reaction times and emotional bias.
Predictive Sustainability Analytics: Models will not only forecast supply/demand but also predict and optimize the carbon footprint and environmental impact of collection, processing, and logistics operations, becoming crucial for ESG reporting and compliance.
Enhanced Material Traceability & Certification: Blockchain combined with IoT and predictive analytics will provide immutable, real-time tracking of scrap origin, composition, and processing history, enabling automated "green steel" or "low-carbon aluminum" certification essential for premium markets.
Regulatory Forecasting & Compliance: AI will analyze legislative trends, policy drafts, and global regulatory announcements to predict future compliance requirements and market access restrictions, allowing proactive adaptation.
The Rise of the "Cognitive Scrapyard": Fully integrated AI systems will autonomously manage yard operations – predicting incoming flows, optimizing sorting (robotics), scheduling processing, managing inventory, and setting dynamic sales prices – maximizing efficiency and profitability with minimal human intervention.
Conclusion:
Predictive analytics is no longer a luxury but a necessity for survival and growth in the volatile scrap metal industry. By moving beyond forecasting into strategic inventory optimization, learning from early adopters, taking pragmatic implementation steps, and preparing for an AI-driven future, scrap metal businesses can transform uncertainty into a sustainable competitive advantage. The revolution is data-driven, and it's accelerating.