Recycling Metal from Electric Vehicle Charging Infrastructure
Explore how metal recycling in EV charging infrastructure unlocks a circular economy—global case studies, policy insights, and cutting-edge tech driving sustainability. Turn e-waste into strategic value.
WASTE-TO-RESOURCE & CIRCULAR ECONOMY SOLUTIONS

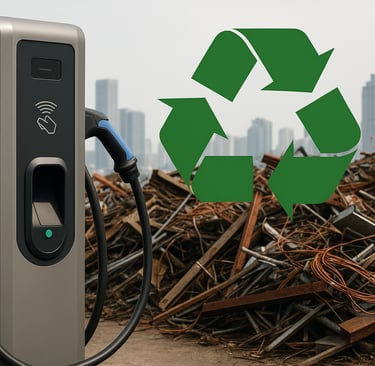
The Imperative of Metal Recycling in EV Charging Infrastructure—Challenges, Opportunities, and Systemic Shifts
The global transition to electric vehicles (EVs) is accelerating at a breakneck pace. With over 26 million EVs on roads worldwide in 2023 and projections suggesting 145 million by 2030 (IEA), the demand for charging infrastructure has surged. Governments and corporations are racing to deploy public chargers, from sleek urban stations to sprawling highway fast-charging hubs. However, this infrastructure boom has unveiled a critical, often overlooked challenge: what happens to these charging systems once they reach end-of-life?
Beneath the polished exteriors of EV chargers lies a complex web of metals—copper, steel, aluminum, and rare earth elements (REEs)—that are both environmentally costly to mine and economically valuable to recover. Without a systemic approach to recycling, the coming wave of decommissioned chargers threatens to exacerbate e-waste crises, strain finite resources, and undermine the sustainability narrative of electrification.
This first part examines the why and how of metal recycling within EV charging infrastructure: the materials at stake, the environmental and economic urgency, and the design and policy shifts needed to build a circular ecosystem.
The Hidden Metal Footprint of EV Charging Systems
A typical EV charging station is a treasure trove of critical metals. For instance:
DC Fast Chargers: Contain 25–30 kg of copper (wiring, connectors), 40–60 kg of steel (structural components), and 200–500 grams of rare earths (neodymium in power electronics, dysprosium in cooling systems).
Level 2 Chargers: Use smaller but still significant quantities, with 5–10 kg of copper and 15–20 kg of aluminum per unit.
Globally, the International Energy Agency (IEA) estimates 30 million public chargers will be installed by 2030. If even 10% are decommissioned annually, 3 million units—carrying ~90,000 metric tons of copper and 180,000 tons of steel—will enter waste streams each year. Without recycling, this represents a $500+ million annual loss in recoverable materials at current market rates, alongside staggering environmental costs.
The Dual Crisis: Environmental Costs and Resource Scarcity
Mining’s Heavy Toll
Virgin metal extraction for EV infrastructure carries steep ecological penalties:
Copper Mining: Produces 2.3–3.5 tons of CO₂ per ton of metal and devastates local ecosystems through open-pit mining.
Rare Earth Mining: Generates radioactive waste (e.g., thorium in monazite sands) and consumes vast amounts of water—1,000 liters per kg of REEs in some regions.
Geopolitical Vulnerabilities
China dominates 85% of global REE processing, while copper reserves are concentrated in Chile (23%) and Peru (10%). Over-reliance on these regions creates supply chain risks as EV adoption grows.
The Recycling Gap: Why Current Systems Fall Short
Despite the urgency, today’s recycling infrastructure is ill-equipped to handle EV charging hardware. Key bottlenecks include:
Design Complexity: Chargers are not built for disassembly. Components like power modules and circuit boards are glued, welded, or coated, making material recovery labor-intensive and costly.
Lack of Standardization: Varying designs across manufacturers complicate large-scale recycling. A 2022 study by Fraunhofer Institute found that disassembling five different charger models took 3–7 hours per unit—a 300% time variance.
Policy Vacuum: Most countries lack regulations mandating charger recycling, leading to ad-hoc disposal. The EU’s Waste Electrical and Electronic Equipment (WEEE) Directive, for example, excludes EV infrastructure, leaving 60% of decommissioned chargers in landfills (Circular Energy Storage, 2023).
Circular Design: Rethinking Chargers for Their Second Life
The solution starts at the drawing board. Design-for-Recycling (DfR) principles are gaining traction, emphasizing:
Modular Architecture: Swappable components (e.g., power converters, cables) that extend lifespan.
Material Simplification: Reducing alloy mixes (e.g., standardized aluminum grades) to streamline sorting.
Digital Tracking: Embedding QR codes or RFID tags to log material composition and disassembly steps.
Companies like Siemens and ABB now publish recyclability scores for new chargers, with targets to achieve 95% recoverability by 2030.
Policy Levers: Accelerating the Shift to Circularity
Early regulatory frameworks are laying the groundwork for systemic change:
EU’s Battery Regulation: Expanding to include EV infrastructure, enforcing minimum recycled content mandates (e.g., 12% recycled copper by 2027).
California’s SB-378: Requires charger manufacturers to fund recycling programs through Extended Producer Responsibility (EPR) fees.
These policies align with broader climate goals. Recycling copper from chargers alone could cut global mining-related emissions by 8 million metric tons of CO₂ annually by 2040 (Rocky Mountain Institute).
From Linear to Circular: The Trillion-Dollar Opportunity
The economic case for recycling is compelling:
Cost Savings: Reusing copper from old chargers is 40% cheaper than virgin mining (CRU Group).
Revenue Streams: Recovered REEs from 1,000 chargers can yield $1.5 million in resale value (Urban Mining Co).
Job Creation: The recycling sector could add 500,000+ jobs globally by 2035 (International Labour Organization).
A Global Movement Takes Shape
The challenges are immense, but so is the momentum. From Norway’s GPS-tracked recycling pilots to AI-driven disassembly lines in Germany, nations and corporations are proving that circularity is not just viable—it’s profitable. Meanwhile, next-gen technologies like cryogenic separation and blockchain traceability are redefining what’s possible in material recovery.
In Part 2, we dive into these pioneering case studies, analyze groundbreaking policies, and explore how cutting-edge innovations are turning end-of-life EV chargers into the foundation of a sustainable electrified future.
Key Takeaways
EV charging infrastructure contains vast quantities of critical, high-value metals currently under-recycled.
Linear disposal models risk resource depletion, supply chain instability, and environmental harm.
Circular design and policy frameworks are emerging as non-negotiable pillars of sustainable electrification.
The economic upside of recycling is a trillion-dollar opportunity waiting to be unlocked.
The race to decarbonize transport isn’t just about building new infrastructure—it’s about ensuring every gram of metal outlives its first use.
Global Case Studies, Policy Insights, and Future Tech Redefining EV Charging Recycling
To fully grasp the enormous potential of EV charging infrastructure recycling, we must widen our lens. Around the world, various governments, cities, and corporations are not only piloting recycling initiatives but also enacting policy frameworks that make recyclability a built-in function of charging solutions—not an afterthought.
This second part explores the macro ecosystem: how nations are responding, which companies are leading the charge (pun intended), and how next-generation technologies are enabling new possibilities in material recovery from electric vehicle infrastructure.
Global Case Studies in EV Infrastructure Recycling
Norway: A Circular Leader in EV Adoption and Infrastructure
Norway isn’t just the world’s leading EV adopter per capita—it’s also making headlines in sustainability-led infrastructure management. The Norwegian Public Roads Administration (NPRA) has launched a pilot program to standardize decommissioning and recycling criteria for EV infrastructure across public roads. The initiative includes GPS tagging of charging stations nearing end-of-life, enabling centralized planning of material recovery.
A 2023 report by the Norwegian Environment Agency revealed that 95% of copper and 87% of steel from decommissioned chargers in pilot runs were successfully recovered. More importantly, the program aims to reduce CO₂ emissions associated with metal production by approximately 15,000 metric tons annually by 2030.
United States: Corporate Initiatives Driving Scalable Impact
In the U.S., infrastructure recycling has found early champions in the private sector. ChargePoint, one of the country’s largest charging network operators, launched a closed-loop refurbishment program in 2022. Instead of scrapping obsolete DC fast chargers, ChargePoint retrieves the high-performing modules—including power converters and communication boards—for re-integration into lower-capacity Level 2 charging stations.
Their internal data shows a 27% cost saving and 34% reduction in material input per refurbished unit, underscoring not only the environmental but also the economic advantage of modular recycling and reuse.
China: Government-Led Standardization Accelerates Recycling
China’s Ministry of Industry and Information Technology (MIIT) published a regulatory roadmap in 2021 mandating design-for-recycling compliance for all new EV infrastructure hardware by 2025. A critical part of this regulation is traceability: each unit must carry a material composition and recyclability score, updated every year.
This public-private engagement model has sped up innovation. Startups like GRINtech have developed automated steel and REE separation lines capable of processing over 100 chargers per hour, now used by state-owned recyclers across Guangdong province.
Policy Benchmarks: Building a Foundation for Sustainable EV Ecosystems
As national EV targets tighten globally, sustainability policies around material use and recovery are gaining traction. Below are compelling frameworks that have sparked meaningful industry change:
Europe’s Critical Raw Materials Act
Adopted in 2023, this legislation compels companies to recover and report recycling rates for a set of 34 critical raw materials, including copper, neodymium, and cobalt. Charging infrastructure—recognized as a high-risk technological sector—must comply with strict end-of-life recovery thresholds:
At least 15% REE recovery by 2025
35% copper recycling rate across infrastructure
Annual EPR compliance reporting by OEMs and recyclers
The policy incentivizes innovation while penalizing subpar recycling outcomes, and is supported by €1 billion+ in funding for technologies enabling automated disassembly and clean material separation.
India’s FAME II & EPR Expansion
While India’s FAME II policy is widely known for subsidizing EVs, its newer extensions in 2024 introduced EV infrastructure recycling protocols under Extended Producer Responsibility. The policy mandates:
Registration of all public charging hardware with official recycling partners
Periodic material recovery audits
Mandatory end-of-life take-back programs by hardware manufacturers
This has led major OEMs like Tata Power and Ather Energy to co-invest in recycling infrastructure and lifecycle management platforms—a trend expected to scale.
Recycling Technology: Expanding the Boundaries of What’s Possible
Tomorrow’s charging infrastructure recycling processes will look nothing like today’s basic disassembly or mechanical shredding protocols. Innovations in robotics, machine learning, and upcycling chemistry are unlocking previously inaccessible value pools.
Let’s break this down by frontier technologies transforming recovery:
AI-Powered Sorting and Disassembly
Autonomous disassembly is one of the most promising frontiers enabling scale. Companies like RecycLAB in Germany are using AI-vision robots to sort, dismantle, and segregate copper wiring, aluminum heat sinks, and printed circuit boards in minutes. These bots also use infrared imaging to distinguish copper from similar-looking alloys, increasing purity rates by nearly 18% compared to human-operated recovery.
Cryogenic Material Separation
Introducing cryogenic freezing during the dismantling process makes ultra-brittle the resin-heavy materials such as PCB substrates. Technologies developed by MIT's Materials Systems Laboratory help freeze and crack open strongly bonded layers, separating complex e-waste structures like REE-dense inverters at scale, without toxic chemicals.
Chemical-Free Rare Earth Recovery
Traditional extraction of neodymium and dysprosium involves corrosive acids and heavy waste generation. But next-gen firms like Urban Mining Co (USA) and Geomega (Canada) have created chemical-free REE recovery loops, using pressure and magnetic separation instead of metallurgic leaching. These systems report over 90% recovery efficiency for recycled REEs with near-zero emissions.
Metrics That Matter: EV Recycling by the Numbers
To understand the scale, let’s quantify what the future of EV infrastructure decommissioning might unleash.
🔹 According to the IEA, over 30 million public chargers will be installed worldwide by 2030. If just 10% are decommissioned annually, we’re looking at 3 million units entering the waste stream every year.
🔹 Each DC charger contains:
25–30 kg of copper
40–60 kg of steel
200–500 g of rare earths (combined)
🔹 At today's market rates, that could yield:
💰 $122.5M in copper annually (assuming $8,000/ton)
💰 $24.6M in steel (at $600/ton)
💰 Up to $375M in REEs (average price of $75,000/ton)—an untapped gold mine
And this doesn’t account for connected grid components whose recycling opportunity is even greater.
The Road Ahead: Future Trends in EV Infrastructure Circularity
Sustainability leaders and OEMs are already looking beyond just recycling. The next wave is recirculation—designing systems that never leave the technological ecosystem. Here’s what to watch for in the next 5 years:
1. As-a-Service Recycling Models
Just like “charging-as-a-service” reshaped how EV owners access power, expect to see “recovery-as-a-service” models where operators pay a monthly fee for recycling logistics, material audits, and performance optimization.
2. Blockchain-Enabled Lifecycle Tracking
Several startups are working on blockchain-based platforms to track each hardware component’s origin, usage history, and recyclability index. This will empower supply chains to make real-time, ethical sourcing and reuse decisions.
3. Digital Material Passports
By 2025, the EU will require Digital Product Passports (DPPs) for electronic devices, including chargers. These smart documents will contain full material disclosure, recovery instructions, and circularity metrics—radically improving recyclers’ ability to process infrastructure efficiently.
Final Thoughts: A Circular Future is a Competitive Advantage
The future doesn't belong to companies that merely deploy charging stations. It belongs to those that design them to come full circle.
EV charging recycling--when done right--doesn't just minimize environmental impact. It maximizes lifecycle value, transforms compliance into differentiation, and turns waste into strategic raw material security.
Companies, governments, and entrepreneurs who embrace these principles will not only impact emissions—but redefine infrastructure sustainability economics.
The circular future of electrification is already underway. The question is: will you lead it or lag behind?
🔥 Want to make sustainability your competitive edge? Subscribe for more insights on circular innovations, ESG strategies, and clean tech growth hacks.