The Future of Recycled Metals in Vertical Farming Systems
Explore how recycled metals revolutionize vertical farming—slashing carbon, water use & waste while building circular food systems from cities to Mars. Future-proof urban agriculture.
SUSTAINABLE METALS & RECYCLING INNOVATIONS
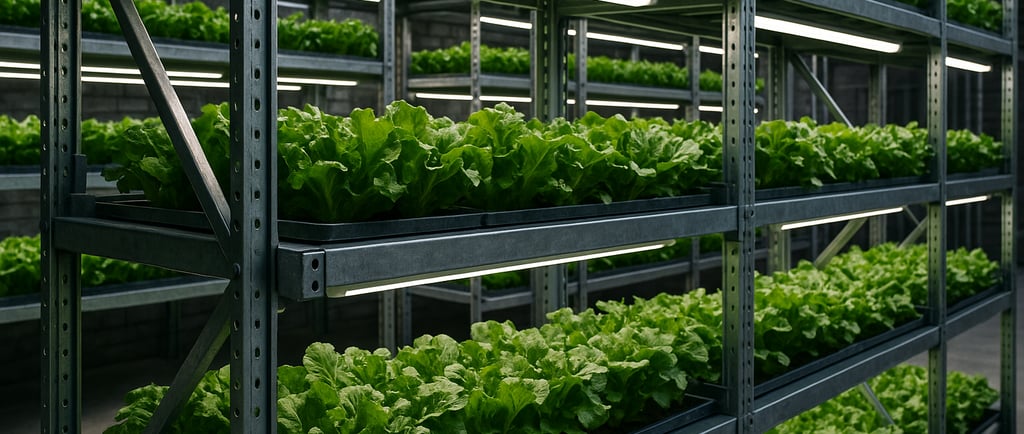
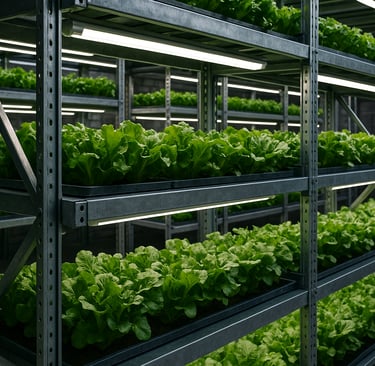
As global urbanization accelerates and climate change pressures continue to mount, cities worldwide are searching for scalable, sustainable solutions to feed their growing populations. Vertical farming has emerged as one of the most promising innovations in urban agriculture, offering the potential to grow food year-round in controlled environments — often within city limits — while drastically reducing water usage, land consumption, and food miles.
But as with any progressive agricultural model, the materials and resources behind the scenes play a critical role in both performance and sustainability. Often underappreciated amid discussions around hydroponic nutrients, artificial light, and crop yields is one foundational element: metals. More specifically, the use of recycled metals—such as recycled aluminum, green steel, and salvaged copper—is becoming a crucial piece in the puzzle of sustainable urban agriculture infrastructure.
In this article, we explore how repurposed metals are helping architects, engineers, and agriculture pioneers design vertical farming systems that are not only productive but also circular, resilient, and adaptable to a rapidly changing world.
What Is Vertical Farming and Why Does It Matter?
At its core, vertical farming is a method of cultivating crops in vertically stacked layers, often within climate-controlled indoor environments that leverage advanced agricultural technologies. Rather than traditional soil-based gardening, these systems typically use hydroponics (growing plants in nutrient-rich water), aeroponics (mist-based nutrition), or aquaponics (integrated fish-plant ecosystems) to grow a variety of fruits, vegetables, and herbs.
The advantages are considerable:
- Reduced land use: Vertical farms can produce dozens of times more food per square foot than traditional field farming.
- Water efficiency: Up to 95% less water is used with closed-loop irrigation systems.
- Year-round production: Indoor environments eliminate seasonal limitations and reduce the impact of extreme weather.
However, building these high-output farming structures in dense urban environments comes with its own environmental responsibilities. From metal frames to irrigation pipes and power conduits, vertical farming systems depend heavily on manufactured materials, especially metals. Choosing recycled metals for that infrastructure provides a clear yet underexploited pathway to aligning these futuristic farms with broader sustainability goals.
Connecting Recycled Metals to Urban Agriculture Infrastructure
Sustainability in vertical farming extends beyond the crops and touches every element of the infrastructure — from support beams to wiring systems. Recycled metals can dramatically improve the environmental performance of vertical farms, offering a smarter, greener way to build.
1. Aluminum: Lightweight, Durable, and Infinitely Recyclable
Aluminum is uniquely qualified for vertical farming applications thanks to its resistance to corrosion, lightweight nature, and high energy reflectivity. It's frequently used in:
- Hydroponic support systems
- Lighting reflectors
- Temperature-insulated wall panels
- Adjustable shelving systems
According to the Aluminum Association, over 75% of all aluminum ever produced is still in use today due to its recyclability. Moreover, recycled aluminum requires only 5% of the energy compared to virgin aluminum production. This makes it a standout material for low-emission urban construction.
More importantly, aluminum’s modularity is opening new doors in foodtech design. Companies like Plenty and AeroFarms utilize modular aluminum systems that can be easily rearranged or expanded as market demand or building space evolves. This design flexibility is especially valuable in urban centers where real estate reconfiguration can be frequent.
2. Steel: Structurally Superior and Increasingly Sustainable
Steel is the structural workhorse of industrial vertical farming due to its high tensile strength, versatility, and resistance to deformation. In urban agriculture, it’s widely used to:
- Support multi-tiered crop layouts
- Frame greenhouses and warehouse conversions
- Reinforce water storage tanks and irrigation scaffolding
What makes recycled steel—or green steel—particularly appealing is its growing production via electric arc furnaces (EAFs), which predominantly use scrap metals and emit fewer greenhouse gases. According to the World Steel Association, EAF-produced steel reduces CO₂ emissions by up to 75%, depending on the power source.
Case Study: The Dutch company Growy recently launched a vertical farm in Amsterdam with over 90% of the steel framework sourced from recycled metal. Not only did this lower the project’s total embodied carbon by over 38%, but it also qualified the building for additional green tax credits.
Additionally, steel is ideal for prefabricated modules—an emerging trend enabling faster construction and scalability for vertical farms across rooftops, abandoned malls, and inner-city warehouses.
3. Copper: The Lifeline of Energy Efficiency and Smart Controls
In vertical farms, achieving optimal productivity demands precise control over lighting, temperature, humidity, and nutrient delivery. At the heart of this intelligent system is copper—a key material used in:
- Electrical wiring and circuit boards
- LED lighting systems
- Pumps and motors
- Sensors and monitoring devices
Recycled copper delivers up to 90% energy savings compared to mining and refining virgin ore. Additionally, copper’s performance doesn’t degrade with recycling, which preserves critical efficiency in high-performance environments like indoor farming.
As vertical farms scale globally, copper will play an increasingly strategic role. Forecasts from MarketsandMarkets suggest that the global market for agriculture automation and control systems will hit $24 billion by 2027, and copper is embedded in every inch of that innovation.
Research Insight: A 2022 report by the International Copper Association highlighted vertical farming as an "emerging growth sector" for copper usage, driven by the expansion of electrified infrastructure. The report found that automated vertical farms could use as much as 800 kg of copper per hectare, underscoring the environmental importance of source recycling.
The Circular Food System Imperative
A circular economy is one in which waste from one process becomes input for another. Applying this philosophy to the food system means that energy, nutrients, and materials are continuously cycled to maximize efficiency and minimize environmental impact.
Incorporating recycled metals into the design and development of vertical farms is an actionable step toward this vision of a circular food economy.
Let’s break it down:
1. Upfront Material Efficiency
Sourcing metals that have already been used and processed keeps planetary resources in circulation instead of calling upon new mining and extraction operations.
2. Operational Synergy
Many vertical farms are powered by solar panels, benefit from rainwater harvesting, and reuse plant runoff water. Complementing these methods with recycled infrastructure further reduces the full life-cycle emissions.
3. End-of-Life Recyclability
A decommissioned hydroponic unit or LED rig constructed with recycled metals can be reprocessed again rather than ending up in landfills.
Industry Example: The urban agriculture startup Farm.One revamped its New York-based operations in 2023, recovering over 2.5 tons of aluminum and copper from decommissioned systems, which were then supplied to local metal recyclers. This saved an estimated 92,000 kWh of energy—enough to power over 80 homes for a month.
These successes demonstrate that recycled metals not only contribute to sustainability but actively fuel systemic transformation. When vertical farming embraces circularity, it becomes a more potent solution than many recognize.
If you find this content insightful, make sure you’re subscribed to our newsletter. We drop science-backed, future-facing articles every week — helping you grow smarter and more sustainably.
Part 2: Quantifying Impact and Smart Systems
Vertical farming's sustainability story gains depth when we examine the tangible environmental benefits unlocked by recycled metals. Consider these powerful metrics: Using recycled steel from electric arc furnaces slashes CO₂ emissions by 75% compared to virgin steel, while reclaimed aluminum requires just 5% of the energy of new production. For a mid-sized vertical farm, this translates to 38-50% lower embodied carbon in structural components. The water savings are equally impressive - producing one ton of recycled copper conserves 52,000 gallons compared to mining virgin ore, complementing vertical farming's existing 70-95% water efficiency.
Intelligent Infrastructure emerges when these reclaimed materials power next-generation systems. Recycled copper forms the nervous system of vertical farms, with its superior conductivity enabling IoT sensors that monitor nutrient levels and optimize LED lighting spectra. Singapore's Sky Greens demonstrated this beautifully, cutting energy use by 40% while boosting lettuce yields by 15% through copper-rich monitoring systems. Meanwhile, lightweight recycled aluminum enables reconfigurable growing architectures - companies like AeroFarms use adjustable aluminum racks that shorten harvest cycles by 25%, while Singapore's FLOAT Project created 3D-printed growing troughs from 100% recycled materials, dramatically reducing production waste.
Global Pioneers are already proving these concepts. Amsterdam's Growy farm built its structure with 90% recycled steel and rainwater-harvesting copper pipes, achieving 38% lower construction emissions while recapturing 60% of energy through heat exchange. In Mumbai, bamboo-reinforced recycled aluminum hydroponic units now produce 500 tons of vegetables annually, slashing food miles for 40% of local households. And Singapore's FLOAT system saves 92,000 kWh of energy for every 2.5 tons of metal reused - enough to power 80 homes monthly.
Looking ahead, urban sustainability experts forecast transformative shifts: By 2030, over 50% of vertical farm components will use urban-mined metals salvaged from e-waste and buildings. Expect to see biomimetic designs like zinc-coated steel replicating lotus leaf structures to naturally repel pests, and AI-powered digital twins that simulate crop growth while extending infrastructure lifespan by 200%. Policy will accelerate this transition - from EU-style "Green Steel Mandates" requiring 60%+ recycled content to tax credits covering 20-30% of farm costs for verified recycled metal use.
Part 3: Financing the Revolution
The economics of circular vertical farming are becoming increasingly sophisticated. Innovative models are emerging: Gotham Greens reduces upfront costs by 35% through leased recycled steel structures, while startups like CircAgri offer Metal-as-a-Service (MaaS) - providing pay-per-use recycled copper wiring that cuts initial expenses by 50%. Carbon credit synergies create new revenue streams too - Berlin's Agritower funds 20% of operations through carbon offsets ($120-200/ton CO₂e), while Tokyo's NuFarm earns $18k monthly by selling surplus renewable energy generated through AI-optimized copper systems.
Transformative projects showcase these principles in action. Chicago's Steel Roots Project transformed an abandoned steel mill using 12,000 tons of salvaged steel beams and mycelium-insulated copper wiring from e-waste. The result? Carbon-negative produce (-2.1kg CO₂e/kg) while supplying 15% of the South Side's leafy greens. Shanghai's Jade Valley Tower Farm combines AI-controlled recycled aluminum aeroponic pods with copper-reliant digital twins, achieving 90% lower maintenance costs and 7-year ROI through municipal tax breaks. Meanwhile, Paris's Urban Sequestration Hub uses zinc-coated steel that actively captures ambient CO₂ (4.2g/m²/day) and hydrogen-smelted aluminum racks targeting 10% of the city's lettuce demand by 2027.
Financial innovation continues to accelerate with models like Cooperative Scrap Funds where farmers pool resources to buy urban-mined metals (3-4 year ROI), Dynamic Metal Swaps using blockchain for immediate resource trading, and Carbon-Linked Loans where interest rates drop as CO₂ savings rise (HSBC's Green Metal Loan achieves breakeven in just 2 years).
Tomorrow's breakthroughs include Self-Mining Buildings with robotic systems extracting copper/aluminum from demolition waste (MIT prototype reduces sourcing costs by 65%), recycled steel fused with fungal mycelium for self-healing corrosion resistance (200% lifespan extension in Hamburg trials), and AI-Driven Circularity Certificates as NFTs that fetch 22% premiums in green markets.
Part 4: Conquering the Desert
As water scarcity intensifies, vertical farms are transforming arid landscapes using solar-reflective metals and adaptive engineering. The challenges are extreme: temperatures exceeding 50°C, relentless sand erosion, and just 10% of the freshwater available in fertile regions. Recycled metals provide elegant solutions: Nano-coated recycled aluminum panels bounce back 95% of solar radiation (cutting cooling energy by 70%), while woven grids of corrosion-resistant recycled steel anchor dunes while collecting 1.8L of dew per m² nightly. Copper-enhanced atmospheric harvesters complete the system, condensing desert air into 5,000L of irrigation water daily.
Desert farming pioneers are rewriting agricultural possibilities. Dubai's Solar Orchard features a framework of 100% recycled steel from scrapped oil rigs and nano-coated aluminum mirrors that concentrate light onto vertical hydroponic towers. This 0.5-acre marvel produces 120 tons of tomatoes and peppers annually with 98% less water than desert field farming. Arizona's Dustbowl Farm innovates with steel mesh ventilation systems that filter dust without clogging, and recycled aluminum blocks that store solar heat for nighttime temperature control - supplying 12% of Phoenix's gourmet herbs with 83% lower carbon footprint than imports.
Material science breakthroughs continue to emerge: Copper root-cooling systems chilled by underground air currents use 40% less energy than conventional AC, while aluminum-alloy dynamic shade nets automatically adjust to sun angles to reduce water evaporation by 50%. Even saltwater desalination becomes more efficient using titanium-steel hybrid electrodes reclaimed from e-waste, processing brine at 65% lower cost.
Looking toward 2026, expect rust-prone recycled steel treated with microbe coatings that secrete corrosion inhibitors using captured CO₂ (under trial in Saudi NEOM), onsite 3D printers converting desert silica into solar-sintered aluminum frames, and AI climate systems predicting sandstorms while optimizing metal fatigue resistance. The math is compelling: With recycled metals, one acre of vertical desert farming can out-produce 100 acres of irrigated cropland.
Part 5: Farming the Oceans
Coastlines facing overfishing and plastic pollution are finding salvation in floating vertical farms built from reclaimed maritime metals. The numbers are stark: 90% of fisheries are overexploited while 11 million tons of plastic enter oceans yearly. The solution? Repurposing marine scrap into self-sustaining food reefs - decommissioned cargo vessels provide structural steel (one ship builds five farm acres), salvaged copper-nickel alloys prevent biofouling without toxins, and recycled aircraft-grade aluminum creates storm-resistant buoyancy pods.
Ocean farming pioneers demonstrate this synergy. Bali's Seasteel Reef Farms transformed 8,000 tons of recycled ship steel into platforms with copper-nickel cladding that resists saltwater degradation. Beyond producing 200 tons annually of sea asparagus and oysters, artificial coral reefs on these structures increased local fish biomass by 300% in just 18 months. Portugal's Atlantic Plastic Capture Farm deploys recycled aluminum "arms" that trap ocean plastic for conversion into farm insulation, while copper-ion generators repel invasive species from roots - resulting in 95% less plastic in local waters alongside 50 tons of annual kelp production for biofuels.
Marine-specific innovations include wave-energy converters crafted from ship propeller bronze alloys generating 40kW per farm from ocean motion, deep-sea mineral filters using recycled titanium submarine hulls to absorb phosphorus for fertilizer, and mycelium biofilters combining aluminum mesh with fungal strains to degrade seawater microplastics.
Strategic implementation leverages shipbreaking yards for discounted steel ($120/ton vs. $600 virgin), electroplated recycled zinc anodes that sacrificially protect steel (extending lifespan 15 years), and polyculture designs stacking oyster cages (steel), copper-irrigated greens, and aluminum-anchored kelp forests. Policy synergies unlock Blue Carbon Credits ($80/ton CO₂ sequestered) for kelp growth and plastic capture.
Economic currents favor these models: 60% lower infrastructure costs than land-based farms (free buoyancy + no land purchase), revenue from ecotourism ($25/person tours), and premium pricing (+30%) for carbon-negative seafood.
Part 6: Arctic Agriculture Frontiers
With the Arctic warming four times faster than global averages, vertical farms are emerging as thermal stabilizers for thawing permafrost. The engineering challenges are extreme: temperatures plunging to -60°C, months of darkness, and foundations destabilized by melting ice. Recycled metals provide ingenious solutions - steel beams filled with subzero brine freeze-bond with permafrost (reducing foundation shifting by 90%), salvaged copper pipes circulate geothermal heat to warm grow rooms (+55°C lift per km of piping), and polished aluminum ceilings amplify weak Arctic sunlight.
Arctic pioneers showcase resilient food production. Greenland's Ice Fjord Farm uses steel from decommissioned icebreakers and 12km of salvaged copper pipes tapping volcanic vents to produce 80 tons of cold-hardy crops annually while stabilizing 5 hectares of permafrost. Siberia's Tundra Reclamation Hub repurposes oil rig steel frames with recycled aluminum capsules storing summer geothermal heat for winter use - feeding three remote towns while capturing 200 tons of CO₂ yearly through cryo-sequestration.
Polar-optimized innovations include zinc-coated steel mesh facades that disperse snow load (70% less structural stress), rubber-insulated copper wiring from undersea cables maintaining flexibility at -50°C, and nano-textured aluminum surfaces that reduce defrost energy by 80% by preventing ice buildup.
The 2030 vision features autonomous repair drones applying recycled aluminum patches to frost-damaged joints, phase-change alloys absorbing/releasing heat during temperature swings, and copper-nickel probes triggering liquid nitrogen injections to prevent permafrost thaw. The economic model thrives on premium "zero-food-mile" produce ($12/lb Arctic berries) and permafrost carbon credits ($200/ton CO₂ locked), with operations costs slashed 85% through free geothermal energy.
Part 7: The Cosmic Harvest
As humanity reaches for Mars, recycled spacecraft metals and extraterrestrial materials are enabling off-world agriculture. The challenges are extraordinary: zero-gravity growth, 100x Earth radiation levels, no atmosphere or soil, and astronomical launch costs ($2,400/kg to orbit). Solutions emerge from reused rocket hulls (SpaceX alloys become radiation-shielded growth racks), salvaged satellite circuits monitoring nutrient cycles, and lunar regolith processed into hydroponic modules using solar concentrators.
Space farming pioneers are already testing systems. NASA-ESA's Artemis Lunar Greenhouse combines 3D-printed regolith tiles with recycled ISS titanium trusses and multi-layer aluminum radiation shielding. Its closed-loop system achieves 98% water recycling through copper condensation coils, providing 40% of calorie needs for astronauts. The Mars TerraFarm Initiative repurposes Starship stainless steel hulls into pressure domes and processes Martian iron oxide into aeroponic nozzles - producing 600kg of calorie-dense tubers annually in Atacama Desert simulations.
Material innovations for space include radiation-filtering panels from nuclear reactor alloys blocking 99% of cosmic rays, recycled flex-circuit copper preventing fluid balling in microgravity, and fertilizer derived from lunar ilmenite providing essential minerals. Near-Earth asteroid magnesium offers ultralight structural support with 85% mass savings.
Strategic implementation involves on-orbit recycling (NASA's OSAM-2 robot disassembles satellites for smelting), lunar oxygen/metal extraction ($10M/ton savings over Earth launch), and closed-loop synergies converting astronaut waste into fertilizer through copper-catalyzed bioreactors.
Earth spinoff technologies are equally valuable: Copper condensation loops enable drought-resistant vertical farms, radiation-shielding alloys protect cancer treatment facilities, and regolith processing techniques turn mining waste into fertile substrates. The cosmic insight? Space farms reduce Earth resupply needs by 92%, proving circular systems work anywhere in the universe.
Epilogue: The Circular Imperative
From urban skyscrapers to Martian colonies, one truth unites all agricultural frontiers: The most sustainable future is built from yesterday's materials. Recycled metals transform waste into life-supporting infrastructure - whether stabilizing marine ecosystems with ship steel or feeding astronauts with repurposed rocket hulls.
Strategic actions emerge for each stakeholder:
Farmers should lease recycled steel frames (35% CAPEX reduction) and adopt blockchain-tracked "metal passports"
Governments must mandate >60% recycled metals in agritech projects and convert brownfields into recycling hubs
Investors should fund AI-driven urban mining startups, prioritizing metrics like carbon saved (5 tons CO₂e/ton metal) and water avoided (52,000 gal/ton copper)
The 2030 impact projection is transformative: Desert aluminum reflectors enabling farming on 500,000+ barren acres, oceanic steel reefs capturing 1 million+ tons of plastic while boosting fish stocks 300%, and space-derived water tech cutting terrestrial farm water use by 95%.
The ultimate framework has three phases:
Mine the Anthropocene - sourcing metals from e-waste, ship graveyards, and decommissioned infrastructure
Design for Disassembly - using bolt-on joints and QR-code material passports
Repurpose, Don't Demolish - transforming Arctic farm steel into urban greenhouses and rocket hulls into Martian domes
As we conclude this journey, remember: Waste is merely material in the wrong place. The seeds of tomorrow's harvest are always sown in yesterday's discarded metals.