The Growth of Modular Recycling Facilities in Remote Markets
Tech-powered modular recycling tackles the global waste crisis in remote regions. Explore decentralized systems, real-world impact, ROI & future trends
WASTE-TO-RESOURCE & CIRCULAR ECONOMY SOLUTIONS
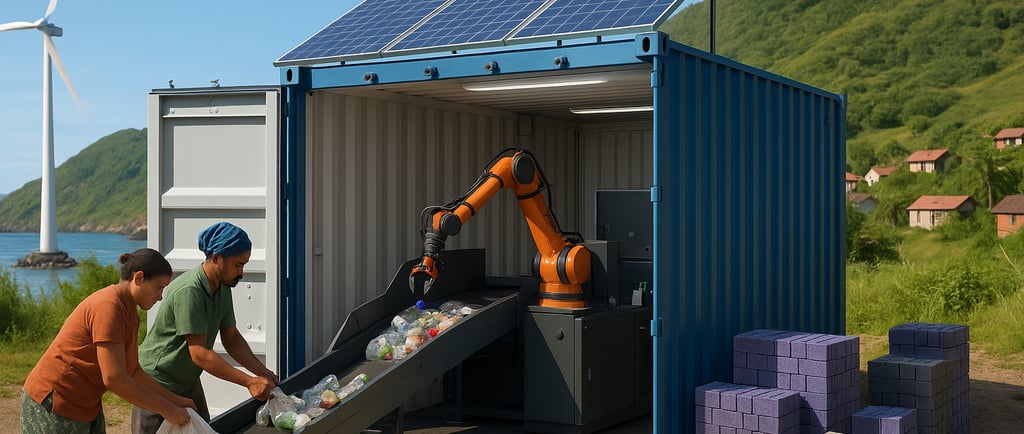
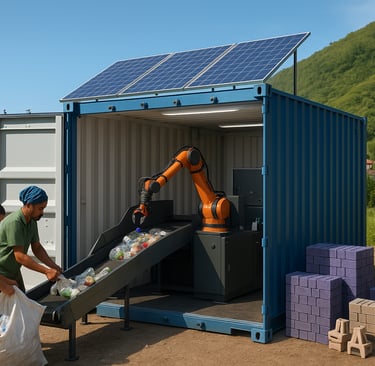
As the global waste crisis accelerates—with humanity generating over 2.24 billion tonnes of solid waste every year according to the World Bank—innovative solutions are becoming essential for reaching underserved and remote regions. One breakthrough innovation is reshaping how communities manage their waste: modular recycling facilities.
Unlike large, centralized recycling plants that demand intensive logistics and infrastructure, modular recycling units bring the plant to the problem. These compact, scalable, and often mobile systems are designed to operate autonomously and efficiently in areas where geography, budget, or politics have long excluded traditional recycling infrastructure.
In this expanded guide, we’ll explore the rapid growth of these next-generation technologies. You’ll learn what modular recycling is, why remote markets are driving adoption, the cutting-edge tech behind these systems, global case studies of success, and what the future holds for the sector. Plus, we’ll uncover ROI metrics for public and private sector stakeholders and provide actionable insights for accelerating deployment, funding, and innovation.
Let’s dive in.
What Is Modular Recycling? A New Paradigm for Waste Management
Modular recycling refers to purpose-built, plug-and-play recycling facilities that are smaller in scale but highly efficient and scalable. These systems are designed for speed of deployment, operational flexibility, and minimal infrastructure demands. Driven by an ethos of decentralization, they usher in a new era of hyperlocal circular economies.
Rather than waiting for waste to be hauled out to distant recycling centers, these facilities can be established directly at the source of waste—whether that’s at an offshore island, mining site, refugee camp, or isolated farming community.
Key Features That Set Modular Recycling Apart
Compact Design: Typically built within shipping containers or modular skeletal structures that are easy to transport.
Zero or Low Grid Dependency: Operable through solar arrays, kinetic energy systems, or compact fuel cells.
Custom Configuration: Units can target multiple waste streams—e.g., PET plastics, HDPE, mixed organics, even e-waste—in one cohesive framework.
Remote Management: Enabled via embedded monitoring systems tied to cloud-based dashboards and AI for remote oversight.
Circular Outcomes: Instead of just processing recyclables, many modular systems can convert waste into usable goods, such as street furniture, bricks, or 3D printing filament.
This shift allows communities to establish "micro recycling economies," where the economic and environmental value of materials is retained locally rather than lost through distant disposal.
Why Remote Markets Are the Ideal Catalyst for Modular Recycling
Large-scale recycling success stories usually come from urban centers. But nearly 30% of the global population—and more than half in Africa and Southeast Asia—live in rural or hard-to-reach areas. These regions often face severe waste management deficiencies.
Here’s why traditional recycling infrastructure often fails in remote markets:
Prohibitive Haulage Costs: Fuel and maintenance expenses for transporting low-value recyclables negate any economic benefit.
Seasonal or Dangerous Transport Routes: In many areas, such as Himalayan villages or Pacific islands, waste can only be transported a few months per year.
Absence of Collection Networks: Without consistent municipal oversight or formal solid waste services, recyclable collection is haphazard or non-existent.
Lack of Capital and Policy Support: Most developing nations allocate less than 0.5% of GDP to environmental infrastructure—leaving gaps that modular systems can fill.
The Distributed Recycling Advantage
By “leapfrogging” heavy infrastructure and transitioning directly to decentralized recycling models, remote communities can:
Prevent Local Environmental Damage: Stopping illegal burning and dumping of waste materials that threaten soil and water safety.
Create Jobs and Circular Microenterprises: Residents become stakeholders in their own solutions.
Generate Local Materials: Plastic bricks for building, mulch for agriculture, or containers recycled into usable goods—produced and used on-site.
Improve Public Health and Sanitation: Especially in areas plagued by open dumpsites that invite disease vectors.
A study from the Ellen MacArthur Foundation shows such localized circular systems can reduce community waste volumes by more than 40% annually when properly implemented.
The Smart Technology Stack Behind Modular Recycling Systems
The impact of modular recycling is intensified by powerful integrations of digital and material technologies. These systems go far beyond "small-scale manual sorting" to incorporate the kind of tech seen in advanced industrial plants.
1. AI-Powered Sorting and Machine Learning Algorithms
By using vision-based AI models trained on millions of image samples, smart sorting belts can now identify PET from HDPE, metals from organic matter, even distinguish different grades of polymers. These systems enable:
Higher purity output (up to 95% sorting accuracy),
Lower labor dependence, and
Adaptive learning, where the system improves over time by ingesting new waste data.
This automation boosts operational throughput, making systems viable even at small scale.
2. Internet of Things (IoT) Sensors and Cloud Control
Real-time monitoring of temperature, humidity, material flow, energy usage, and contamination levels help operators monitor remotely. These insights feed cloud analytics systems, allowing:
Proactive maintenance,
Real-time reporting for donors and regulators,
Predictive inventory/logistics oversight.
One Norwegian startup, Plast365, has demonstrated how IoT dashboards reduced downtime in modular units operating above the Arctic Circle by 40%.
3. Renewable and Autonomous Energy Integration
Many of the most successful deployments are off-grid, harnessing:
Solar arrays sized for continuous daytime operation and nighttime battery storage,
Micro wind turbines in breezy coastal regions,
Diesel-solar hybrids in lower sunlight geographies.
This energy resilience shifts the value equation significantly for undeveloped regions.
4. In-Situ Product Development Tools: 3D Printing & Molding
Taking circularity to the next level, modular recyclers increasingly include integrated fabrication capabilities:
Replicabots in South Asia built open-source 3D printers that manufacture tools and fixtures from upcycled waste.
Some systems include injection molding mechanisms to produce consistent building products, like LEGO-style pavers or prosthetic limbs made from milk jugs.
These value-added outputs make modular systems more than just waste management tools—they become community manufacturing hubs.
Scaling the Solution - Deep Dives into Impact, Challenges, and the Future of Modular Recycling
Part 1 laid the foundation: modular recycling is a paradigm shift, bringing hyper-local, tech-enabled circularity to the world's most underserved regions. Now, we delve deeper, examining tangible impacts, confronting scaling hurdles, and forecasting the evolution of this critical sector.
Global Case Studies: From Proof-of-Concept to Community Transformation
Moving beyond theory, these ground-level examples showcase the real-world power and adaptability of modular systems:
Plastic Archipelago Solution - Spermonde Islands, Indonesia:
Challenge: Island communities drowning in plastic waste, no collection services, prohibitive transport costs to mainland recycling.
Solution: Solar-powered containerized unit processing PET/HDPE/PP via AI sorting, shredding, and pelletizing. Integrated injection molder produces fishing gear buoys, construction stakes, and household items.
Impact: 60% reduction in visible shoreline plastic waste within 18 months. Local co-operative formed, selling pellets to mainland manufacturers and finished goods locally. ROI: Payback period of ~3 years based on pellet sales and avoided environmental cleanup costs (estimated $150k/year). Key Tech: Salt-air resistant components, low-maintenance shredders, rainwater collection for processing.
Circular Economy in the Arctic - Tuktoyaktuk, Canada:
Challenge: Remote First Nations community facing rising waste volumes, fragile Arctic ecosystem, high fuel costs for waste haulage (1,000+ km to landfill).
Solution: Wind/solar hybrid modular unit focusing on organics (composting for local greenhouse agriculture) and plastics (shredding/flaking for use in community construction projects as insulation filler and low-grade lumber substitute).
Impact: Diverted 70% of community waste from long-haul transport. Created 5 local jobs. Reduced greenhouse vegetable import costs by 30%. ROI: Primarily social/environmental; payback estimated at 8-10 years via avoided haulage fees ($250/tonne) and food security benefits. Key Tech: Cold-weather composting bioreactors, robust energy storage, satellite-based IoT for remote monitoring.
E-Waste Microfactory - Kibera, Kenya:
Challenge: Massive informal e-waste dumping in Nairobi's largest informal settlement, hazardous manual dismantling, lost valuable materials.
Solution: Compact, secure unit with robotic disassembly arms (trained via ML on local e-waste streams), safe PCB processing, and precious metal recovery via compact hydrometallurgy. On-site 3D printers use recovered ABS/PC for market stalls and utility parts.
Impact: Formalized and safer work for 20+ former informal recyclers. 95% material recovery rate vs. <60% previously. Reduced lead/mercury contamination. ROI: ~2-year payback projected from recovered gold, copper, and high-value plastic sales. Key Tech: Safety enclosures, adaptive robotics, compact chemical recovery with closed-loop systems.
Economic & Environmental Impact: Quantifying the Value Proposition
The case studies hint at the compelling ROI, but broader metrics solidify the argument:
Municipal/Public Sector ROI:
Cost Avoidance: Reduces long-haul transport (often $100-$500/tonne) and landfill tipping fees ($50-$150/tonne). A single unit processing 1 tonne/day can save a remote municipality $50k-$200k+ annually.
Job Creation: Each unit typically creates 3-10 direct local jobs (operation, maintenance, product sales) plus indirect opportunities in collection/logistics.
Health Cost Savings: Reduction in open burning/dumping lowers respiratory illnesses and water contamination, saving public health expenditure.
Private Operator/Investor ROI:
Lower Capex: Modular units cost $150k-$500k vs. $5M-$50M+ for traditional plants, enabling faster entry.
Faster Deployment: Operational in weeks/months, not years, accelerating revenue generation.
Revenue Streams: Sale of recycled materials (flakes, pellets), value-added products (bricks, filament, goods), waste processing fees, carbon credits.
Profit Margins: Efficient units processing high-value streams (PET, metals) can achieve 20-40% gross margins. Payback periods range from 2-7 years depending on scale, location, and waste stream value.
Environmental ROI (Beyond Diversion):
Carbon Footprint Reduction: Eliminates long transport emissions. A unit processing 1 tonne/day locally vs. hauling 500km can save ~100 tonnes CO2e/year. Use of renewables amplifies this.
Resource Conservation: Keeps valuable materials (plastics, metals, organics) in productive use locally, reducing virgin resource extraction.
Ecosystem Protection: Prevents leakage into oceans, forests, and farmland, preserving biodiversity and soil/water quality.
Challenges to Scale: Navigating the Roadblocks
Despite the promise, significant hurdles remain for widespread adoption:
1. Financing the Frontier:
High upfront costs are prohibitive for cash-strapped municipalities and NGOs in target regions. Traditional lenders perceive high risk.
Solutions Needed: Blended finance models (development bank guarantees + impact investment), leasing/PPPs, results-based financing (payment for verified tonnes diverted), microloans for community co-ops.
2. Technical Resilience & Maintenance:
Harsh environments (extreme temps, humidity, dust, corrosion) strain equipment. Limited local technical expertise causes downtime.
Solutions Needed: Ruggedized "extreme environment" packages, modular redundancy, comprehensive remote diagnostics (AI-driven predictive maintenance), robust training programs with AR support, localized spare part networks.
3. Feedstock Consistency & Quality:
Variable waste streams (contamination, mix) challenge automated sorting and efficient processing, impacting output quality and economics.
Solutions Needed: AI sorters with continuous learning, modular pre-processing units (washing, shredding), community education programs tied to collection incentives, adaptable processing lines.
4. Policy & Regulatory Fragmentation:
Lack of supportive waste management policies, unclear standards for recycled products (especially building materials), and bureaucratic hurdles impede deployment.
Solutions Needed: Advocacy for "sandbox" regulations in pilot zones, development of clear modular system certification standards, harmonization of end-product standards (e.g., for plastic lumber).
5. Market Development for Outputs:
Creating stable local demand for recycled products (flakes, pellets, finished goods) is critical for long-term viability.
Solutions Needed: Government procurement mandates for recycled content in public projects, incubators for circular micro-enterprises, partnerships with manufacturers seeking local feedstock, consumer awareness campaigns.
Predictive Outlook: The Modular Recycling Evolution
The trajectory points towards an increasingly sophisticated and integrated future:
1. Hyper-Specialization & Multi-Stream Integration:
Units will evolve beyond "general recyclers" to highly optimized configurations for specific regional waste profiles (e.g., "Tourist Island PET+Organics" vs. "Mining Camp Metals+Plastics"). Seamless integration of processing for 3-5 key streams within a single modular footprint will become standard.
2. AI & Robotics Dominance:
Vision systems will achieve near-human sorting accuracy (>98%) for complex streams. Robotics will handle more disassembly, cleaning, and product fabrication tasks, reducing labor intensity and improving safety (especially for e-waste/toxics).
3. Blockchain for Traceability & Trust:
Immutable ledgers will track waste origin, processing steps, and final product composition, enabling premium pricing for verified circular materials and facilitating carbon credit verification.
4. Advanced Material Recovery:
Modules for chemical recycling (pyrolysis, depolymerization) will become more compact and efficient, allowing modular systems to handle previously "unrecyclable" plastics and textiles directly at source, producing virgin-quality feedstocks or fuels.
5. Emerging Global Standards & Certification:
Expect rapid development of:
ISO Standards for Modular Systems: Covering safety, environmental performance, output quality, and data reporting (ISO/TC 297 for Factory Modules is a starting point).
Circular Product Certifications: Standards for products made from modularly recycled materials (e.g., "Modular Circular Certified" labels), building consumer trust.
Carbon Methodology Approval: Streamlined methodologies for quantifying and verifying the carbon savings of distributed recycling, unlocking carbon finance.
UNEP/World Bank Guidelines: Frameworks for integrating modular recycling into national waste management strategies and development funding.
The Imperative: From Niche to Norm
Modular recycling isn't just a stopgap; it's the foundational infrastructure for a truly circular economy, particularly where traditional models fail. The technology is proven. The economic and environmental case is compelling. The challenge now is systemic: mobilizing finance, building adaptive policies, developing robust markets, and fostering global standards.
The next 5-10 years will be decisive. With concerted effort from governments, investors, innovators, and communities, modular systems can move from pioneering pilots to becoming the default solution for waste management across vast swathes of the planet. The result? Cleaner environments, empowered communities, conserved resources, and a significant step towards mitigating the global waste crisis – one hyper-local, tech-powered micro-facility at a time. The future of waste is distributed, intelligent, and circular.