The Hydrogen Economy’s Hidden Metal Demands
Unveiling platinum, nickel & titanium's critical roles in hydrogen infrastructure. Explore supply risks, sustainable sourcing imperatives, and investment pathways for the hydrogen economy.
SUSTAINABLE METALS & RECYCLING INNOVATIONS
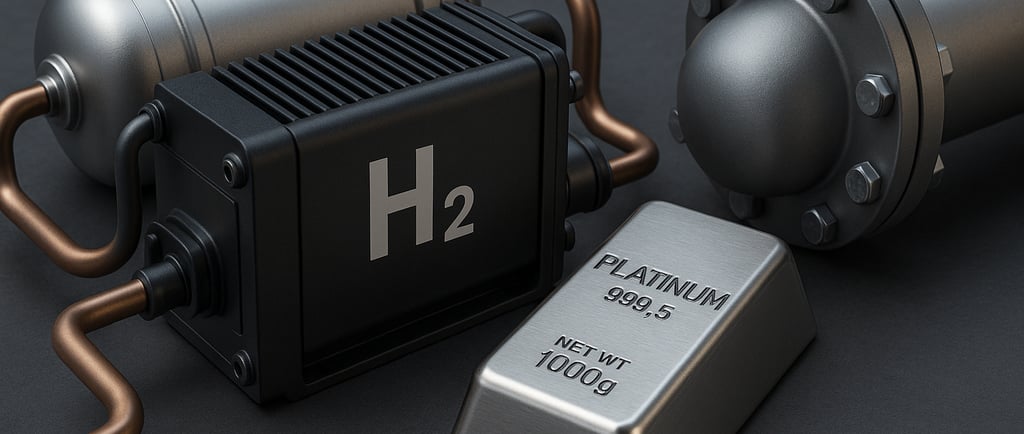
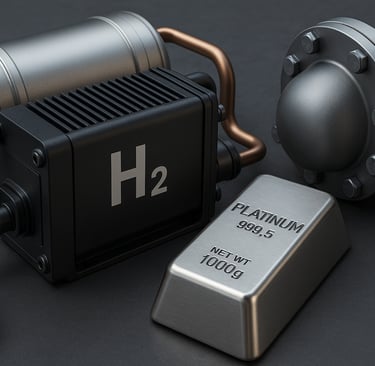
1. What is the Hydrogen Economy?
The hydrogen economy represents a paradigm shift toward a low-carbon future by utilizing hydrogen as a central vector for clean energy deployment. As global emissions targets tighten and fossil fuel dependence wanes, hydrogen’s flexibility becomes increasingly attractive. It functions as a versatile, storable, and transportable fuel with applications across sectors—spanning fuel-cell electric vehicles (FCEVs), industrial decarbonization, and long-duration energy storage.
Hydrogen’s categorization into grey, blue, and green reflects the energy sources and methodologies used in production:
Grey hydrogen is derived from natural gas via steam methane reforming (SMR), resulting in high carbon emissions.
Blue hydrogen follows the same production path but incorporates carbon capture and storage (CCS) technologies to mitigate climate impact.
Green hydrogen, considered the cleanest variant, is synthesized through electrolysis powered by renewable energy sources like solar and wind.
Although green hydrogen is garnering the most attention in policy and investment circles—especially in Europe’s REPowerEU plan, the U.S. Hydrogen Energy Earthshot, and Japan’s Basic Hydrogen Strategy—the full-scale deployment of these technologies hinges on much more than access to renewable electricity. It requires a robust physical infrastructure underpinned by specialized materials.
Emerging projects like NEOM’s $8.4 billion green hydrogen plant in Saudi Arabia and Australia’s Asian Renewable Energy Hub are not only scaling clean power sources but signaling an industrial appetite that will soon test the resilience and scalability of hydrogen-supporting metal ecosystems.
2. Why Metals Matter in the Hydrogen Ecosystem
To many, hydrogen may seem like an ephemeral gas with few physical dependencies. But behind this invisible fuel lies a foundation of metal-intensive components and systems that shape how hydrogen is created, stored, and converted into usable energy.
From an engineering perspective, the hydrogen economy interpolates into four critical segments:
Generation – Through water electrolysis using electrolyzers
Storage – Often under high pressures or in cryogenic states
Distribution – Pipelines, tube trailers, or tanker ships
Utilization – In industrial processes or fuel cells
All four stages are underpinned by high-performance materials—especially platinum, nickel, and titanium—each playing indispensable roles.
Contextual Significance of Hydrogen-Related Metals:
Electrolyzers: Deploy nickel and platinum as electrocatalysts.
Fuel cells: Rely on platinum for oxygen reduction and hydrogen oxidation reactions.
Storage vessels: Incorporate titanium linings to prevent hydrogen permeation and corrosion.
Distribution systems: Utilize titanium and nickel alloys to maintain structural integrity under extreme atomic stress.
The convergence of green hydrogen expansion and clean technology deployment is creating a crucible of demand growth for these specialty metals. According to a 2023 report by BloombergNEF, electrolysis system costs are expected to fall nearly 60% by 2030—but this will only be achieved if material inputs remain available and affordable.
3. Platinum: The Catalyst Behind Hydrogen Fuel Cells
As the prime proton exchange membrane (PEM) fuel cell catalyst, platinum has earned its status as the hydrogen economy’s most symbolically and financially valuable metal.
PEM fuel cells function by converting hydrogen into electricity through a redox reaction, releasing water as the only byproduct. Platinum facilitates the efficiency of this reaction by serving as both the hydrogen oxidation catalyst (anode) and the oxygen reduction catalyst (cathode).
Key Metallurgical Advantages:
High catalytic surface area: Increases reaction velocity
Thermal and electrical conductivity: Improves efficiency
Resistance to acid corrosion: Enhances system longevity in harsh environments
Platinum’s dual role in both PEM fuel cells and PEM electrolyzers underscores its systemic importance. Each 100-kW fuel cell vehicle may contain up to 30–60 grams of platinum, depending on technological design and cost optimization.
Demand Curve & Supply Risk:
The World Platinum Investment Council (WPIC) estimates that hydrogen consumption will account for up to 20% of total platinum demand by 2030. Factors driving this include:
Subsidized rollouts of fuel cell buses in China
Japan’s strategy to deploy 800,000 FCEVs by 2030
Growing PEM deployments in grid-scale hydrogen hubs
On the supply side, about 72% of global platinum output emanates from South African mines, which are subject to labor disputes, power outages, and environmental critiques. Adding geopolitical stack risk, Russia supplies 13%—recent years have shown how quickly regional tensions can distort global material flows.
To counter this, R&D initiatives are exploring alternative catalysts, including palladium, ruthenium, or operating advancements that reduce platinum loading per cell. However, most of these are still in early-stage research or present their own price and supply chain issues.
4. Nickel: Powering Green Hydrogen via Electrolyzers
Nickel may not have the premium status of platinum, but it is no less critical for expanding access to green hydrogen. Alkaline and solid oxide electrolyzer cells (SOECs) rely heavily on nickel-based catalysts due to their cost-effectiveness and durability.
Functions Within Electrolyzers:
In alkaline electrolyzers, nickel serves as a primary cathode or anode material due to its excellent water-splitting capability under alkaline conditions.
In SOECs, it is typically used as part of ni-YSZ (nickel-yttria-stabilized zirconia) composites for high-temperature hydrogen production.
These attributes make nickel indispensable in systems designed for continuous, high-output hydrogen production, such as:
Gigascale hydrogen hubs
Thermal energy storage systems
Industrial ammonia or steel manufacturing retrofits
The Supply Tension:
The International Energy Agency (IEA) forecasts an over 100% increase in nickel demand by 2040—driven by surging demand from EV battery producers and now electrolyzer manufacturers.
Recent case studies show the crossover threat more vividly:
Tesla's Gigafactory in Nevada consumes vast quantities of Class 1 nickel, further tightening supply.
European Commission’s Green Deal Industrial Plan earmarks nickel as a “strategic raw material,” reinforcing sourcing urgency.
The potential dual squeeze—between batteries and hydrogen—may create bottlenecks unless efficient recycling methods and secondary nickel sources, such as urban mining or scrap recovery, are scaled.
5. Titanium: The Unseen Guardian of Hydrogen Integrity
While platinum and nickel capture headlines, titanium operates as the silent sentinel ensuring hydrogen's safe journey from production to point-of-use. Its unique properties make it irreplaceable in critical logistics infrastructure facing hydrogen's most aggressive challenge: embrittlement and permeation.
Why Titanium Reigns Supreme:
Embrittlement Resistance: Hydrogen atoms diffuse into most metals, causing catastrophic cracking. Titanium's hexagonal close-packed (HCP) structure inherently resists this degradation.
Permeation Barrier: Titanium forms a dense, passive oxide layer (TiO₂) that drastically reduces hydrogen gas diffusion compared to steel or aluminum.
Corrosion Champion: Exceptional resistance to saltwater, acids, and high-pressure environments encountered in pipelines, offshore platforms, and maritime transport.
Strength-to-Weight Advantage: Critical for mobile storage (tube trailers) and cryogenic tanks, where weight impacts efficiency.
Evolving Applications Driving Demand:
High-Pressure Storage & Transport: Type IV composite tanks (carbon fiber shell) require titanium polymer liners for permeation resistance in FCEVs and tube trailers (350-700 bar).
Long-Distance Pipelines: Repurposing natural gas pipelines for hydrogen mandates internal titanium cladding or liners to prevent embrittlement in welds and joints – a key focus for EU and US backbone projects.
Liquid Hydrogen (LH2) Tankers: Cryogenic temperatures (-253°C) demand titanium alloys (like Ti-5Al-2.5Sn ELI) for inner containment vessels due to superior toughness and near-zero thermal contraction.
Electrolyzer & Fuel Cell BOP: Heat exchangers, pump impellers, and valve components exposed to wet hydrogen or aggressive electrolytes rely on titanium grades like Gr 2 or Gr 7.
The Cost-Supply Conundrum:
Titanium's high extraction and processing costs (Kroll process) remain a barrier. Concentrated production (China, Russia, Japan, Kazakhstan) and complex aerospace supply chains create vulnerability. Scaling hydrogen logistics requires either significant cost reductions in titanium manufacturing or breakthrough composite liners – neither is guaranteed near-term. Projects like the Port of Rotterdam's hydrogen import terminal highlight the non-negotiable role of titanium in global H2 trade.
6. The Urgency of Sustainable and Secure Metal Sourcing
The hydrogen economy's promise hinges on the ethical and resilient supply of its foundational metals. Current trajectories reveal alarming vulnerabilities demanding immediate, coordinated action.
The Looming Supply-Demand Chasm:
Platinum Group Metals (PGMs): 70%+ supply concentration (South Africa/Russia) faces ESG risks (water, energy, labor) and geopolitical instability. Hydrogen demand could consume >30% of annual PGM supply by 2040 (IEA SDS).
Nickel: Surging demand from EVs and electrolyzers strains Class 1 nickel supply. Indonesian laterite ore (dominant source) requires energy-intensive HPAL processing, raising carbon footprint concerns.
Titanium: Geopolitical risks (Russia supplies ~15% of sponge) and high embedded emissions challenge "green" hydrogen's lifecycle credentials if sourcing isn't addressed.
Beyond Mining: The Sustainability Imperative:
ESG Risks: "Green" hydrogen tarnished by metals mined with high carbon emissions, water stress, or human rights abuses is unacceptable to investors and consumers. Traceability is paramount.
Circularity Gap: Recycling rates for PGMs in autocatalysts are high (>90%), but hydrogen applications (dispersed fuel cells, electrolyzers) present new collection challenges. Nickel and titanium recycling for hydrogen tech is nascent.
Resource Nationalism: Export restrictions (e.g., Indonesia's nickel ore ban) and critical mineral lists (EU, USA) signal intensifying competition. Hydrogen strategies must include material security pacts.
Pathways to Resilience:
Accelerated Recycling R&D: Designing fuel cells & electrolyzers for disassembly, developing efficient hydrometallurgical processes for complex components.
Primary Production Innovation: Lower-emission titanium reduction (e.g., MIT's FFC Cambridge process), bioleaching for nickel, renewable-powered PGM refining.
Certification & Standards: Robust schemes (e.g., IRMA for mining, potential H2-specific material standards) to verify sustainable and ethical sourcing throughout the chain.
7. Strategic Investment Pathways: Building the Metal-Hydrogen Nexus
Investors play a pivotal role in de-risking the material foundation of the hydrogen economy. Capital must flow strategically across the value chain to ensure scalability and sustainability.
Key Investment Verticals:
Upstream Resource Security:
Mining & Refining: Targeted investments in diversified, ESG-leading PGM, nickel, and titanium sponge producers. Focus on jurisdictions with stable policy and high ESG standards (e.g., Canada, Botswana, Norway).
Exploration Tech: Funding advanced geophysical surveying and AI-driven mineral discovery to identify new ethical deposits.
Midstream Processing & Alloy Development:
Alternative Processing: Backing companies commercializing lower-cost, lower-emission metal production (e.g., green hydrogen-based reduction for titanium).
Advanced Alloys: Investing in R&D for high-performance, material-efficient alloys (e.g., low-PGM catalysts, embrittlement-resistant steels with reduced Ti/Ni content).
Circular Economy Enablers:
Recycling Infrastructure: Scaling dedicated hydrogen tech recycling facilities and reverse logistics networks.
Urban Mining Tech: Supporting innovators in efficient recovery of high-purity metals from complex end-of-life hydrogen components.
Material Innovation & Substitution:
Catalyst R&D: Venture capital for startups developing ultra-low PGM loadings, PGM-free catalysts (e.g., Fe-N-C), or novel earth-abundant materials.
Advanced Composites: Funding R&D into next-gen permeation barriers (e.g., graphene-enhanced polymers) to reduce titanium dependency.
Investment Instruments & Risk Mitigation:
Public-Private Partnerships (PPPs): Co-funding pilot plants for sustainable refining or large-scale recycling.
Specialized ETFs & Funds: Focused on "Hydrogen Materials" or "Energy Transition Metals."
Offtake Agreements & Strategic Reserves: Industry consortia securing long-term metal supply; government stockpiling for critical minerals.
Derisking Mechanisms: Loan guarantees for mining projects meeting high ESG bars, insurance products for geopolitical supply disruption.
8. Final Takeaways: Material Foundations Dictate Hydrogen Ambitions
The scale and speed of the hydrogen economy's growth are inextricably linked to the availability, affordability, and sustainability of its core metals. Ignoring this material dimension risks stranding assets, inflating costs, and undermining environmental goals. Key conclusions emerge:
No Hydrogen Scale Without Metals Scale: Gigawatt-scale electrolysis, continent-spanning pipelines, and millions of FCEVs require order-of-magnitude increases in platinum, nickel, and titanium production. Supply chains must be built now to avoid 2030 bottlenecks.
Sustainability Starts at the Mine: "Green" hydrogen's credibility demands metals sourced and processed with minimal environmental impact and strong social governance. ESG performance is non-negotiable for investors and consumers.
Innovation is Multi-Pronged: Success requires parallel tracks:
Optimizing Incumbents: Reducing PGM loadings, improving titanium utilization efficiency.
Enabling Circularity: Building robust global recycling systems for hydrogen tech.
Pursuing Alternatives: Aggressive R&D into lower-cost, abundant material substitutes (long-term horizon).
Geopolitics is Material: Concentration of supply (PGMs in Southern Africa, Nickel in Indonesia, Titanium sponge in China/Russia) creates significant risk. Diversification through new sources, strategic stockpiles, and international partnerships is essential for energy security.
Collaboration is Key: Solving this requires unprecedented collaboration:
Governments: Setting clear critical mineral policies, funding R&D, enabling permitting.
Industry: Forming consortia for secure sourcing, standardizing designs for recyclability.
Investors: Directing capital towards sustainable primary production, recycling tech, and material innovation.
Researchers: Accelerating discovery of new materials and processes.
The Bottom Line:
Metals are not merely inputs; they are the bedrock enablers of the hydrogen transition. Prioritizing resilient, responsible, and innovative material supply chains isn't optional – it's the prerequisite for realizing the hydrogen economy's vast potential. The time for integrated action across the metal-hydrogen nexus is now.