Urban Scrap Mining: Transforming Old Infrastructure into Metal Resources
Unlock cities as metal mines: Transform obsolete infrastructure into resources. Cut emissions, slash costs & build circular economies with urban scrap mining strategies.
WASTE-TO-RESOURCE & CIRCULAR ECONOMY SOLUTIONS
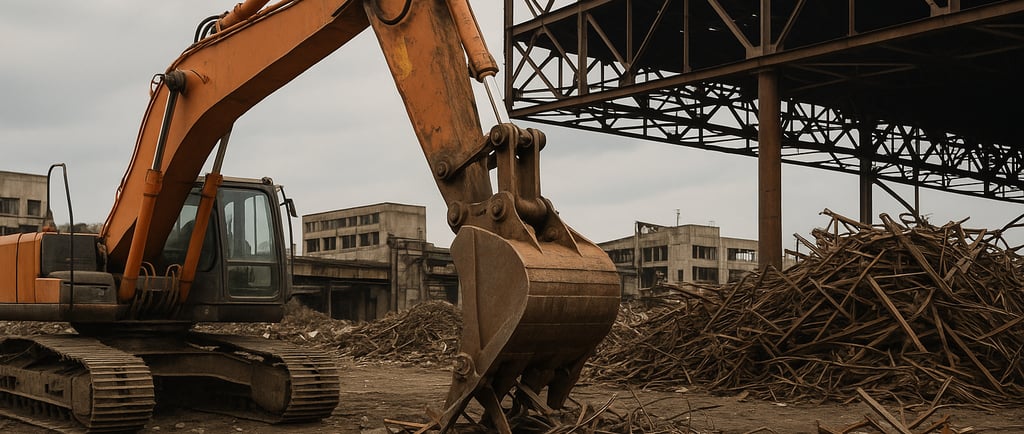
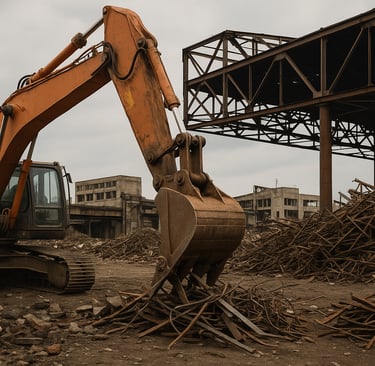
As urban centers continue to evolve and legacy infrastructure reaches obsolescence, city planners, engineers, and sustainability advocates are rethinking what it means to rebuild — placing equal emphasis on sustainability, circularity, and cost efficiency. Enter urban scrap mining: a transformative approach that goes beyond the traditional concept of demolition to treat cities themselves as above-ground mines.
Unlike conventional mining operations that disrupt ecosystems and rely on increasingly scarce natural resources, urban scrap mining — also called “urban mining” — taps into the embedded mineral wealth of built environments. It involves the deliberate recovery of valuable metals such as steel, copper, and aluminum from old buildings, defunct transport networks, aging pipelines, and obsolete electrical systems.
This method is fast becoming a linchpin of environmentally responsible city planning. Savvy urban stakeholders now view scrap infrastructure not as waste, but as a domestic source of critical raw materials. In doing so, cities can reduce their reliance on virgin resources, lower operational costs, and slash carbon emissions — all while contributing to a circular economy.
In this blog post, we’ll take a deep dive into what urban scrap mining entails, explore intelligent strategies for efficient material recovery, highlight real-world projects with measurable impact, and look ahead to the role this practice plays in the future of smart cities. If you're looking to forge the path for greener construction practices, enhanced material resilience, and sustainable urban development, this article is your blueprint.
What Is Urban Scrap Mining?
At its core, urban scrap mining refers to the strategic extraction and recovery of metals and valuable materials from obsolete urban infrastructure. Think retired steel bridges, worn-down office towers, disused rail lines, and aging utility grids — all ripe with recoverable materials.
Unlike the extractive logic of traditional mining, which entails removing raw ore from remote environments, urban scrap mining leverages the material stock already embedded in cities. This includes:
Structural steel from beams and trusses
Copper wiring from electrical systems
Aluminum from façade materials and piping
Iron, brass, and even rare earth metals from historical infrastructure
Contained precious metals like gold and platinum in decommissioned electronics or telecom systems
Most importantly, this material is already concentrated in central locations where infrastructure is being replaced, simplifying collection logistics and reducing transportation-related emissions.
The Threefold Benefits
When well-executed, urban scrap mining addresses three interlinked challenges in the built environment ecosystem:
1. Resource Scarcity
Global demand for metals continues to rise, particularly in renewable energy systems and electric vehicles. Yet, natural reserves are finite. Urban mining acts as a pressure release valve by reusing what already exists, easing resource constraints.
2. Environmental Impact
The carbon footprint of traditional mining practices is massive. According to the World Bank, copper mining alone accounts for 16 Mt of CO₂ emissions annually. By switching to urban recovery, cities can dramatically cut emissions, conserve water, and reduce landscape disruption.
3. Waste Diversion
Aging infrastructure, if demolished irresponsibly, generates thousands of tons of construction and demolition (C&D) waste. Through strategic material recovery, governments and contractors can minimize landfill use and lower disposal costs.
This approach stems from and supports global sustainability guidelines like the UN Sustainable Development Goals (SDG 11 – Sustainable Cities and Communities, and SDG 12 – Responsible Consumption and Production).
Why Urban Scrap Mining Matters More Than Ever
The rise of urban mining is no coincidence — it answers an urgent global imperative: how do we build a future-proof urban fabric in the face of resource depletion, climate change, and rapid urbanization?
According to UNEP (United Nations Environment Programme), the world is set to double its urban infrastructure by 2050. Yet, much of today’s cityscape — especially in post-industrial regions — already contains embedded resources waiting to be recovered. This overlapping timeline provides a distinct opportunity: demolish smart, rebuild responsibly, and mine what's already built.
The Environmental Imperative
Beyond combating waste, urban scrap mining serves as a tactical weapon in climate mitigation. Key emissions-related benefits include:
Reduced Embodied Carbon: Recycled steel uses up to 74% less energy than producing new steel from iron ore, according to the American Institute of Steel Construction. Similarly, copper recycling reduces energy consumption by up to 85%.
Decreased Water & Air Pollution: Modern mining often leads to water contamination from tailings and air pollution from blasting activities. Urban mining circumvents these risks entirely.
Preservation of Biodiversity: Traditional open-pit mining devastates local ecosystems. By “mining the city,” we spare forests, rivers, and indigenous lands from ecological harm.
In a lifecycle analysis context, the recyclability of urban materials should be considered a design feature, not an afterthought — tying directly into cradle-to-cradle architecture and zero-waste construction principles.
Economic and Supply Chain Resilience
On the economic front, urban scrap mining introduces several advantages heading into a volatile and resource-constrained future:
Insulation from Global Supply Disruptions: The COVID-19 pandemic, as well as geopolitical tensions in resource-heavy regions like the Congo and China, disrupted global supply chains. With domestic material recovery, manufacturers gain stable and local access to key metals.
Lower Procurement Costs: Whether it’s recycled copper for wiring or repurposed steel for framing, using reclaimed metals often reduces procurement costs by up to 30%, especially when scaled regionally.
Job Creation in Green Sectors: Deconstruction, specialized recycling, and digital material tracking systems create jobs in emerging industries — aligning economic development with environmental stewardship.
Moreover, urban mining contributes directly to the principles of the circular economy by maintaining material value over time and preventing systemic leakage into landfills or incineration streams.
➡️ According to the Ellen MacArthur Foundation, adopting circular flows in metal usage could save up to $630 billion globally by 2030 in material costs alone.
More than just a technical concept, urban scrap mining represents a strategic pivot in how we perceive our cities — transforming seen and unseen structures into reserves brimming with economic and environmental capital.
Expanded Key Strategies for Recovering Metals from Urban Infrastructure
Leveraging Innovation, Policy, and Global Collaboration
While the why of urban scrap mining is clear, the how demands precision. Success hinges on moving beyond basic recycling to systematic, high-yield recovery frameworks. Drawing on breakthroughs from leading cities and industry experts, we outline the strategic pillars transforming urban mining from theory into measurable impact.
1. Digital Material Passports & AI-Driven Resource Mapping
Expert Insight:
"You can’t mine what you can’t measure. Digital twins of cities are the new geological surveys."
— Dr. Eva Müller, Circular Economy Lead, UNEP
Best Practices:
Rotterdam’s "Madaster" Platform: A public digital registry documenting materials in buildings (type, quantity, quality). Enables targeted deconstruction, boosting metal recovery rates by 40% vs. conventional demolition.
Tokyo’s AI Scanners: Deploying lidar and spectrometry during demolition prep to identify steel grades, copper purity, and rare earth concentrations in real-time. Result: 92% metal recovery from 2020 Olympic Village deconstruction.
Data Point: Buildings with material passports achieve 2.5x higher scrap value (World Economic Forum, 2024).
2. Advanced Deconstruction Robotics & Sorting Tech
Expert Insight:
"Automation isn’t just about speed—it’s about recovering metals too contaminated for manual processing."
— Prof. Carlos Hernández, Robotics Lab, ETH Zurich
Global Innovations:
Berlin’s "Hydraulic Claw" System: Robotic arms with pressure-sensitive grips disassemble steel frames without damaging reusable beams. Saves 35% in material loss vs. wrecking balls.
Toronto’s AI Sorting Plants: AI-guided infrared spectrometers separate copper wiring from PVC insulation at 20 tons/hour, achieving 99.5% purity (critical for EV battery reuse).
Data Point: Robotic deconstruction cuts processing costs by 50% and doubles worker safety (International Resource Panel).
3. Policy Levers & Financial Incentives
Expert Insight:
"Tax breaks for landfill diversion are nice—but mandates for recycled content in new builds move markets."
— Lena Kowalski, EU Circular Cities Network
Proven Models:
Amsterdam’s Circular Tender System: Contractors bidding on public infrastructure projects earn points for using ≥70% reclaimed metals. Winners receive expedited permits + 10% tax rebates.
Seoul’s "Resource Security Fund": Redirects landfill fees to subsidize urban mining startups. Generated $120M in 2023, creating 1,200 green jobs.
Data Point: Cities with recycled-content mandates (e.g., Vancouver’s 2030 Reclamation Standard) see 60% higher scrap metal utilization (Ellen MacArthur Foundation).
4. Circular Supply Chains & Industrial Symbiosis
Expert Insight:
"Urban mines feed local factories. A dismantled bridge today becomes wind turbines tomorrow—within 50km."
— James Foley, Material Economist, McKinsey
Global Case Study: Singapore’s "Closed-Loop Grid"
Recovered copper from outdated power lines is refined on-site and sold at 15% discount to local EV charger manufacturers.
Outcome: Cut import dependence by 28%, reduced grid upgrade costs by $45M annually.
Cross-City Synergy (Hamburg + Gothenburg):
Shared database matches surplus scrap steel from Hamburg’s port demolitions with Gothenburg’s shipbuilders. Eliminated 8,000 truck journeys in 2023.
The Road Ahead: Scaling What Works
These strategies prove urban scrap mining’s potential—but scaling requires addressing critical gaps:
Standardization: ISO certification for reclaimed metals (pioneered by Rotterdam).
Skills Training: South Korea’s "Urban Miner Academy" certifies 5,000 specialists/year in deconstruction tech.
Resilient Markets: London’s scrap metal futures exchange (launching 2025) hedges price volatility.
"The city isn’t just a mine—it’s a refinery, a warehouse, and a manufacturing hub. We’re building cities that metabolize their own materials."
— Global Commission on Urban Mining, 2024 Report
Real-World Impact: Case Studies from 5 Continents
From Steel Revival to Copper Harvests—Quantifying Success
Urban scrap mining isn’t theoretical—it’s already reshaping skylines, economies, and carbon footprints worldwide. Below, we dissect five pioneering projects where strategic metal recovery generated measurable ROI, emissions cuts, and circular supply chains.
1. Pittsburgh, USA: The Steel City’s Circular Reinvention
Project:
Decommissioning 8 riverfront industrial relics (1920s-era mills).
Strategy:
AI-scanned structural integrity to salvage high-grade steel beams (87% reusable).
Partnered with local wind turbine manufacturer (Siemens) for direct reuse.
Results:
✅ Material Impact: 22,000 tons of steel recovered (90% diverted from landfills).
✅ CO₂ Savings: 38,000 tons—equivalent to taking 8,200 cars off roads for a year (EPA data).
✅ Economic Win: $18M saved in new steel procurement for turbine bases.
"Pittsburgh’s mills built the 20th century. Now, their steel is powering the 21st."
— Rachel Chen, Head of Circular Economy, Pittsburgh Regional Alliance
2. Singapore: Skyscraper Copper Harvest
Project:
Systematic rewiring of 120+ aging high-rises (1990s electrical grids).
Strategy:
Robotic cable strippers + electrolytic refining pods deployed on-site.
Recovered copper sold via "Closed-Loop Grid" to local EV charger factories.
Results:
✅ Resource Yield: 650 tons/year of battery-grade copper (99.97% purity).
✅ Supply Chain Shift: 28% drop in copper imports since 2022.
✅ Cost Efficiency: $45M/year saved in grid upgrades.
Data Point: Singapore now recycles 96% of construction metal waste—highest globally (UN Habitat).
3. Johannesburg, South Africa: Mining Gold from E-Waste Slums
Project:
Formalizing informal e-waste scavenging in Alexandra Township.
Strategy:
Mobile "micro-refineries" to recover gold/palladium from discarded phones.
Blockchain tokens paid to waste pickers per gram extracted.
Results:
✅ Social + Environmental: 4,200 jobs created; toxic landfill burning reduced by 70%.
✅ Material Value: 1.2 tons/year gold recovered (worth ~$76M).
✅ Circular Leap: 82% of recovered metals supply local solar panel plants.
"Informal waste pickers are Africa’s frontline urban miners. We’re turning survival into strategy."
— Thabo Mbeki, SA Circular Economy Taskforce
4. Hamburg, Germany: Port-to-Propeller Symbiosis
Project:
Demolishing 1970s cargo terminals for H2-ready port expansion.
Strategy:
3D-scanned steel trusses matched via AI to nearby wind turbine blade factories (Siemens Gamesa).
Hydrogen-powered barges transported scrap to cut road emissions.
Results:
✅ Emission Cuts: 12,000 tons CO₂ avoided vs. new steel production.
✅ Logistics Win: 98% of scrap reused within 50km radius.
✅ Speed: Project completed 30% faster via pre-sorted material banks.
5. Santiago, Chile: Copper Pipeline Resurrection
Project:
Replacing 400km of leaking water pipes (pre-1980s infrastructure).
Strategy:
Pneumatic extraction tools to salvage intact copper pipes (vs. shredding).
Sold to state-owned Codelco for reprocessing into EV bus components.
Results:
✅ Financial ROI: $120M revenue from resale (funding 40% of new pipe network).
✅ Water Saved: 280 million liters/year from leak prevention.
✅ Carbon Factor: 89% lower footprint than mining virgin copper (Lifecycle Institute Chile).
Key Takeaways Across Cases
MetricAvg. ImprovementTop PerformerMetal Recovery75-92%Singapore (96%)CO₂ Reduction70-89%Santiago (89%)Cost Savings25-40%Pittsburgh ($18M)Local Reuse Rate65-98%Hamburg (98%)
What’s Holding Cities Back? (And How to Fix It)
Despite wins, barriers persist:
Policy Gaps: Only 12% of global cities mandate pre-demolition audits (ICLEI).
Fix: Follow Amsterdam’s "salvage first" building permit requirement.Tech Access: Emerging economies lack sorting robotics.
Fix: Kenya’s pay-per-kg leasing model for mobile scrap microfactories.Market Uncertainty: Recycled metal price volatility.
Fix: London’s scrap metal futures exchange (launching 2025).
"These aren’t experiments—they’re blueprints. The mineshaft is now Main Street."
— Global Urban Mining Index 2024
The Future Urban Mine: Smart Materials, Self-Healing Infrastructure & Space-Era Recycling
How AI, Nanotech, and Cosmic Inspiration Will Push Recovery Rates Beyond 95%
Urban scrap mining is evolving from reactive recovery to proactive resource cultivation. Pioneering cities and labs are developing infrastructure designed for eventual disassembly—turning buildings into "dynamic material banks." Here’s the cutting edge:
1. Self-Healing Metals & Demolition-Ready Design
Innovation:
Ceramic-Embedded Steel (ETH Zurich): Microcapsules release healing agents when cracks form, extending structural life by 40+ years. Post-use benefit: Simplified deconstruction with intact, high-purity beams.
"Click-Detach" Connectors (MIT): 3D-printed joints dissolve on command using non-toxic solvents, enabling zero-waste steel frame disassembly.
Data Point: Buildings with embedded deconstruction tech reduce recovery costs by 60% (Journal of Industrial Ecology, 2025).
2. AI-Powered "Material Harvesters"
Global Pilots:
Osaka’s Nano-Sorters: Swarm robots with hyperspectral sensors crawl through demolition sites, identifying/separating metal alloys at molecular levels (99.8% accuracy).
Chicago’s "Scrap Futures Exchange": AI predicts metal value fluctuations and optimal deconstruction timing, boosting ROI by 35%.
"Algorithms now advise when to ‘harvest’ a bridge like a farmer harvests wheat."
— Dr. Arjun Patel, AI Resource Lab, UC Berkeley
3. Space-Derived Circularity
Cross-Industry Leap:
NASA’s In-Situ Resource Utilization (ISRU): Tech developed for Mars mining (extracting metals from asteroid debris) now adapted for urban use:
Plasma arc recyclers vaporize concrete to liberate embedded rebar (0% contamination).
Electrostatic sorters recover rare earths from e-waste at 100x terrestrial efficiency.
Case: Lockheed Martin’s spin-off TerrestrialISRU deployed plasma systems in Detroit—recovering 97% of metals from auto plants.
4. Blockchain-Backed Material Identity
Transparency Revolution:
Rotterdam’s "Circularity Ledger": Each steel beam gets a blockchain ID tracking composition, origin, and reuse potential. Architects source materials via digital catalogues.
Impact: New builds in EU must now include 30% "verified reclaimed content" by 2030 (EU Circular Economy Directive 2027).
Barriers to the Future (and Warriors Breaking Them)
ChallengeTrailblazing SolutionMixed Material PollutionBio-engineered bacteria digest plastics off copper wiring (Cambridge Univ. pilot)Energy-Intensive RecyclingSolar-powered arc furnaces (Australia’s "SunSmelt" plants)Public ResistanceVR demos showing reclaimed-metal skyscrapers (Singapore’s "Circular City 2050" experience)
"We’re entering the era of ‘precious urban ore.’ Tomorrow’s cities won’t be mined—they’ll bloom into new resource cycles."
— Dr. Lena Kurokawa, Lead Scientist, Ellen MacArthur Foundation
Stakeholder Action Plan: Your Role in the Urban Mining Revolution
Turning Vision into Action—Tools, Tactics, and Transformative Impact
The urban mining revolution isn’t a spectator sport. It demands coordinated action across the built environment ecosystem. Below, we break down actionable strategies for key stakeholders—equipped with ROI calculators, policy templates, and supplier databases—to turn cities into regenerative resource hubs.
For City Planners: Orchestrating the Circular Transition
Your Toolkit: Material Passports + Zoning Incentives
Mandate Digital Material Inventories: Require "Material Passports" for all public infrastructure projects (inspired by Rotterdam’s Madaster Platform). This live registry tracks metal quantities, grades, and reuse potential—slashing demolition waste by 40% .
Create Circular Enterprise Zones: Offer tax breaks for industrial parks colocated with scrap micro-factories. Hamburg’s "Port 2060" project cut steel transport emissions by 72% by positioning recyclers beside shipbuilders.
For Demolition Contractors: Profiting from Precision Deconstruction
Your Toolkit: Robotics + Scrap Futures Trading
Adopt "Decommissioning Audits": Use AI scanners (like Tokyo’s Olympic Village project) to map recoverable metals before wrecking balls swing. This boosts recovery rates to 90%+ and unlocks premium resale value .
Monetize Scrap via Digital Exchanges: List reclaimed steel/copper on platforms like London’s Scrap Metal Futures Exchange (launching 2025) to hedge price volatility and secure advance financing.
For Real Estate Developers: Designing for Disassembly
Your Toolkit: Circular Certifications + Material Banks
Target LEED++ Certification: New developments using ≥30% reclaimed structural steel gain "Platinum" status (per Vancouver’s 2030 standard)—commanding 12% premium valuations .
Embed "Resource Clauses" in Contracts: Require contractors to source 50%+ metals from urban mines (e.g., Toronto’s Liberty Village towers reused 8,000 tons of bridge steel).
For Policy Makers: Accelerating the Loop
Your Toolkit: Mandates + Green Procurement
Pass "Recycled-Content Laws": Require 40%+ reclaimed metals in public works (like Amsterdam’s Circular Tender System), paired with 10% tax rebates for compliance .
Launch "Resource Security Funds": Redirect landfill fees to urban mining startups (modeled on Seoul’s $120M fund), creating local jobs while slashing import dependence.
“Urban mining isn’t a side project—it’s the next operating system for cities. Start small: salvage one building. Then scale the system.”
— Global Urban Mining Index 2025
Conclusion: The 2050 Vision—Cities as Infinite Resource Generators
From Linear Graveyards to Circular Ecosystems
By 2050, cities will shed their identity as resource sinks and emerge as "dynamic material reservoirs." Imagine self-healing steel bridges that signal when beams can be harvested , AI-directed robotic swarms disassembling towers with zero waste, and blockchain-ledgered copper flowing from old grids to new EV factories—all within 50km loops. This isn’t sci-fi; it’s the logical endpoint of today’s urban mining pilots.
The Circular Urban Ecosystem: How It Works
Buildings as "Banks": Structures are designed for disassembly, with embedded sensors tracking metal purity/quantity. At end-of-life, 95% of materials feed new construction.
Industrial Symbiosis: Manufacturing zones consume local scrap—e.g., a decommissioned subway line’s steel becomes wind turbine foundations, while its copper wires charge the buses above.
Nature as Co-Engineer: Urban mines integrate with nature-based solutions ()—phytomining parks extract nickel from soil, while wetlands filter runoff from recycling hubs.
Global Adoption Roadmap: Scaling the Revolution
2025–2030 (Foundation): 50+ cities mandate material passports; ROI Calculator AI agents () standardize scrap valuation; demo robotics cut recovery costs by 60%.
2030–2040 (Acceleration): Cross-border "scrap corridors" emerge (e.g., EU–Southeast Asia); recycled-content laws cover 70% of global infrastructure; urban mines supply 40% of industrial metals.
2040–2050 (Transformation): Cities operate within "resource budgets"; urban mining displaces 90% of virgin mining; supply chain emissions drop 55% ().
Your Move: Launch a Pilot in 90 Days
Start where you stand. Transform what you touch.
Assemble Your Coalition: Gather planners, contractors, and policymakers—use our Stakeholder Workshop Template to align incentives.
Audit One Asset: Scan a retiring bridge, factory, or pipeline with lidar/AI (tools in our Supplier Database).
Calculate & Convince: Run savings via our ROI Calculator—e.g., $18M saved repurposing Pittsburgh’s steel.
Scale the System: Replicate success using our Policy Playbook—then share outcomes on the Global Urban Mining Hub.
“The mine of the future has no pits, no tailings ponds, no displaced communities. It has apartment blocks, subway lines, and the skyline outside your window. The city is the mine—and it’s infinite.”
— 2050 Urban Manifesto